Joining HDPE (high-density polyethylene) pipes is a critical aspect of constructing a reliable and leak-free piping system. There are several methods available for connecting HDPE pipes, each with its own advantages and considerations. This comprehensive guide will introduce you to the different types of HDPE connections, including butt fusion, electrofusion, mechanical connections, and flanged connections, highlighting their characteristics, applications, and installation requirements.
Butt Fusion Connection
Butt fusion is a widely used method for joining HDPE pipes of the same diameter. The process involves heating the pipe ends and then pressing them together under pressure, resulting in a seamless and strong fusion bond. Here are some key points about butt fusion connections:
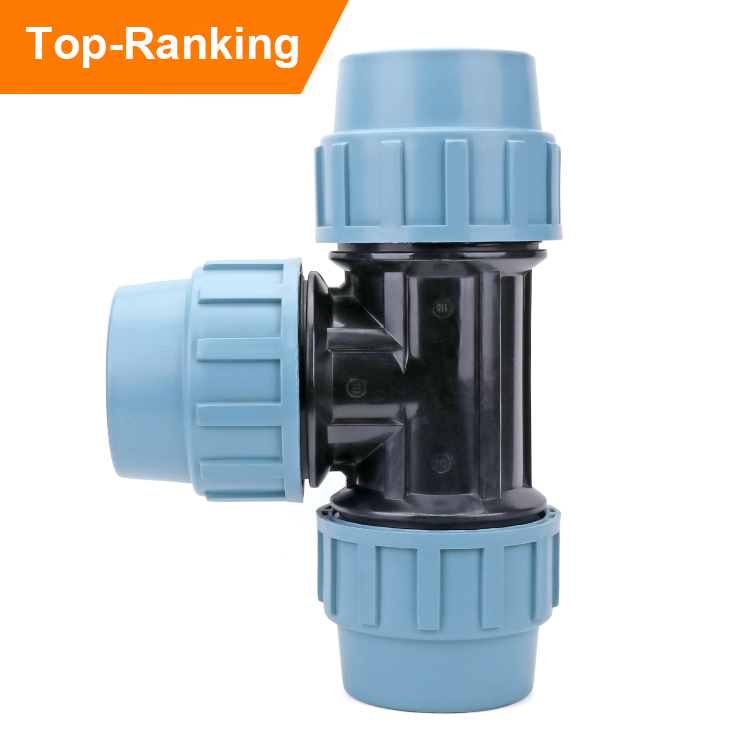
- Advantages: Butt fusion connections provide excellent strength, integrity, and leak resistance. They are suitable for high-pressure applications and offer a smooth and continuous interior surface, minimizing flow resistance.
- Application: Butt fusion connections are commonly used in water distribution systems, gas transmission lines, industrial piping, and other applications that require durable and leak-free joints.
- Installation: Specialized equipment, such as butt fusion machines, are required for heat fusion. The proper heating and cooling times, pressures, and fusion parameters should be followed to ensure a successful connection.
Electrofusion Connection
Electrofusion is a method that utilizes electrofusion fittings to join HDPE pipes. These fittings contain embedded heating elements that melt the HDPE material and create a fusion bond when an electric current is applied. Here are some key points about electrofusion connections:
- Advantages: Electrofusion connections offer similar benefits to butt fusion, providing strong and leak-free joints. They are ideal for complex piping layouts, as they allow for easy and precise alignment of pipes.
- Application: Electrofusion connections are commonly used in gas and water distribution systems, as well as in applications where merging or branching of pipes is required.
- Installation: Electrofusion requires specialized electrofusion machines and fittings, along with proper training and certification. The installation process involves cleaning the pipe ends, inserting the fitting, and applying the correct fusion parameters to create a reliable joint.
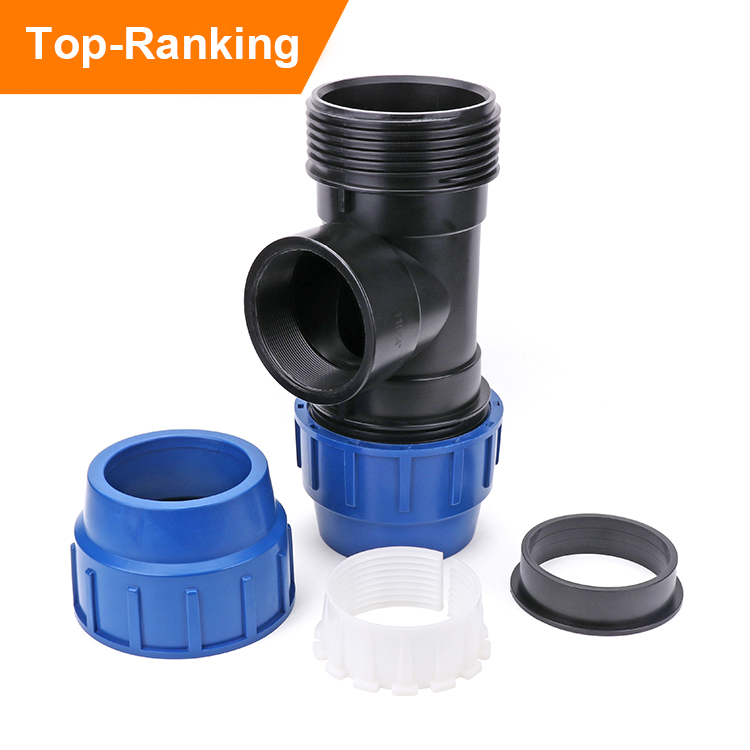
Mechanical Connection
Mechanical connections offer a convenient alternative to fusion methods and involve the use of mechanical fittings to join HDPE pipes. These fittings typically utilize compression mechanisms, clamps, or bolts to secure the pipes together. Here are some key points about mechanical connections:
- Advantages: Mechanical connections provide versatility and ease of installation, allowing for quick and temporary connections, repairs, or modifications. They do not require specialized equipment or training.
- Application: Mechanical connections are suitable for low-pressure applications, temporary installations, or situations where disassembly and reassembly may be necessary.
- Installation: The installation process varies depending on the type of mechanical fitting used. Compression fittings require tightening the compression rings, while clamps or bolts are used in other types. Proper tightening torque and alignment are essential for a secure and leak-free connection.
Flanged Connection
Flanged connections involve joining HDPE pipes using flange adapters or stub flanges that are bolted together. This method allows for the connection of HDPE pipes to other types of pipes or equipment with matching flange dimensions. Here are some key points about flanged connections:
- Advantages: Flanged connections offer versatility and compatibility with various pipe materials. They allow for easy disassembly and reassembly, making them suitable for applications requiring frequent maintenance or equipment replacement.
- Application: Flanged connections are commonly used in industrial applications, such as chemical processing, mining, and water treatment facilities.
- Installation: Flanged connections require careful alignment of the flange faces, proper gasket selection, and accurate torqueing of the bolts. Following the recommended bolt tightening sequence and torque values is crucial for ensuring a reliable and leak-free connection.
Conclusion
Understanding the different types of HDPE connections is essential for selecting the appropriate method for joining HDPE pipes. Butt fusion and electrofusion connections provide seamless and strong joints suitable for high-pressure applications. Mechanical connections offer versatility and ease of installation for temporary or low-pressure applications. Flanged connections allow for compatibility with other pipe materials and facilitate easy disassembly and reassembly. Each connection method has its own advantages, considerations, and installation requirements. By selecting the right connection method and following proper installation procedures, you can create a robust and reliable HDPE piping system.