IFAN factory 30+ years manufacture experience support color /size customization support free sample.Welcome to consult for catalog and free samples.This is our Facebook Website:www.facebook.com,Click to watch IFAN’s product video.Compared with Tomex products, our IFAN products from quality to price are your best choice, welcome to buy!
When it comes to gas pipeline installations, safety, reliability, and efficiency are paramount. Using the right materials is essential for ensuring that gas distribution systems perform optimally while minimizing risks. One of the best choices for these types of installations is HDPE fittings. Known for their strength, durability, and resistance to harsh environmental factors, HDPE fittings are rapidly becoming the go-to solution for many industries, including gas pipelines.
In this article, we will explore the benefits of using HDPE fittings for gas pipeline installations, highlighting their advantages over other materials like PPR fittings, and how they contribute to efficient, safe, and cost-effective gas distribution systems.
What are HDPE Fittings?
High-Density Polyethylene (HDPE) fittings are plumbing components made from a tough and resilient plastic material. HDPE is widely used in various industries due to its superior resistance to chemicals, corrosion, and extreme temperatures. HDPE fittings include a variety of components such as elbows, tees, reducers, flanges, and couplings, all designed to connect and secure HDPE pipes in various piping systems.
In the context of gas pipeline installations, HDPE fittings are specifically engineered to handle the high-pressure demands and potential risks involved in transporting natural gas, propane, and other fuel gases.
Key Benefits of HDPE Fittings for Gas Pipeline Installations
1. Leak-Free Performance
One of the most critical factors in gas pipeline installations is ensuring that the system is completely leak-free. Even a minor leak can pose significant safety hazards, including the risk of fire, explosion, and environmental damage. HDPE fittings are ideal for gas pipelines because they can be fused together using heat fusion welding techniques, creating a strong, homogenous bond between the pipes and fittings.
Unlike other materials, HDPE fittings do not rely on mechanical joints or seals that can wear out over time. Instead, the fusion process ensures a seamless and permanent connection that is resistant to leakage, making HDPE fittings an excellent choice for gas pipeline systems that require the highest level of safety.
2. Chemical and Corrosion Resistance
Gas pipelines are often exposed to harsh conditions, including moisture, soil chemicals, and other corrosive elements. Over time, metal pipes can corrode, leading to costly repairs and potential safety risks. HDPE fittings, on the other hand, are naturally resistant to corrosion and chemical degradation.
They can withstand exposure to a variety of chemicals commonly found in the soil and environment, including acids, alkalis, and salts, ensuring a longer lifespan for gas pipelines. In comparison, PPR fittings are less resistant to certain chemicals, making them less suitable for environments where corrosion is a concern.
3. Durability and Longevity
Gas pipeline systems need to last for decades, and the materials used must be able to endure the test of time. HDPE fittings offer exceptional durability, with a life expectancy of 50 years or more when properly installed and maintained. The ability of HDPE fittings to resist wear and tear, extreme temperatures, and physical stress makes them an excellent long-term investment for gas pipeline infrastructure.
PPR fittings, while durable for certain applications, typically have a shorter lifespan and are more suitable for water distribution systems rather than gas transport.
4. Flexibility and Impact Resistance
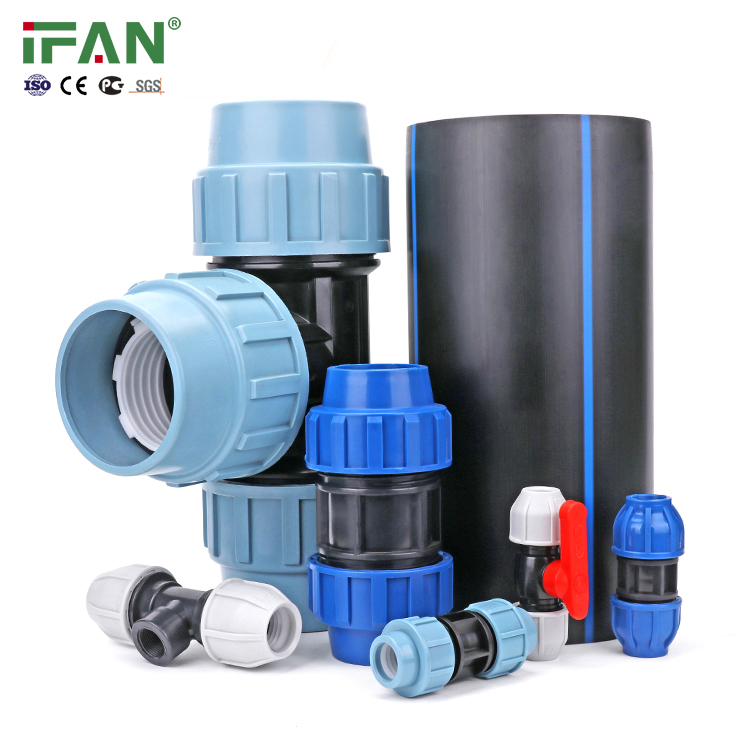
Another significant advantage of HDPE fittings is their flexibility. HDPE pipes and fittings can withstand impacts, pressure fluctuations, and ground movement without cracking or breaking. This makes them particularly suitable for underground gas pipeline installations, where the system may be exposed to shifting soil, seismic activity, or other external forces.
In contrast, PPR fittings are rigid and more susceptible to cracking under physical stress. They do not offer the same flexibility and resilience, which makes HDPE fittings the preferred choice for gas pipelines that need to withstand environmental stresses.
5. Ease of Installation
HDPE fittings are lightweight and easy to handle, which simplifies the installation process. The fusion welding technique used to join HDPE fittings is fast, efficient, and does not require specialized tools or labor-intensive methods. This not only speeds up the installation but also reduces labor costs and potential errors during construction.
PPR fittings, on the other hand, often require threaded or glued connections, which can be time-consuming and prone to installation errors. Additionally, HDPE fittings do not require sealing agents, further reducing the complexity of the installation.
6. Cost-Effectiveness
Although HDPE fittings may have a higher upfront cost than PPR fittings, they offer significant long-term savings. The low maintenance, durability, and resistance to corrosion of HDPE fittings reduce the need for frequent repairs, replacements, and downtime. This translates into lower overall costs over the life of the pipeline.
While PPR fittings are more affordable initially, they may require more frequent repairs and maintenance, especially in harsh environments. For industries looking to maximize cost-effectiveness and minimize downtime, HDPE fittings present a better long-term investment.
7. UV Resistance
In some gas pipeline installations, the piping system is exposed to direct sunlight. UV radiation can weaken and degrade certain materials over time. HDPE fittings offer excellent UV resistance, ensuring that the pipeline system remains intact even with prolonged exposure to sunlight.
PPR fittings are not as UV resistant and are typically used for indoor applications or areas with minimal sunlight exposure. This makes HDPE fittings the better choice for outdoor or above-ground gas pipeline systems.
8. Environmentally Friendly
As the world becomes more focused on sustainability, the environmental impact of materials used in infrastructure is increasingly important. HDPE fittings are made from recyclable materials, making them a more eco-friendly option compared to traditional metals or non-recyclable plastics. Their long lifespan and recyclability reduce waste and contribute to the overall sustainability of the project.
PPR fittings are also recyclable but do not offer the same level of environmental benefits as HDPE fittings in terms of longevity and resistance to harsh conditions.
HDPE Fittings vs. PPR Fittings for Gas Pipeline Installations
While both HDPE fittings and PPR fittings offer certain advantages, they are better suited to different applications. HDPE fittings excel in high-pressure, high-stress environments, making them the preferred choice for gas pipelines that need to withstand harsh conditions, chemical exposure, and potential impacts. Their durability, leak-free performance, and UV resistance make them a top choice for gas pipeline installations that prioritize safety and longevity.
PPR fittings, on the other hand, are more suitable for water distribution systems and less demanding applications. While they are durable and resistant to corrosion, they do not provide the same level of protection against chemicals, extreme temperatures, or mechanical stress as HDPE fittings.
Conclusion
For gas pipeline installations that require efficiency, safety, and long-term performance, HDPE fittings are the ideal choice. Their superior durability, chemical resistance, flexibility, and ease of installation make them the go-to material for creating reliable and leak-free gas distribution systems. While PPR fittings have their place in water distribution, HDPE fittings are far better equipped to handle the demands of gas pipelines, ensuring that they operate safely and efficiently for decades to come.
Frequently Asked Questions (FAQs)
1. What makes HDPE fittings ideal for gas pipeline installations?
HDPE fittings are ideal due to their leak-free performance, chemical resistance, durability, flexibility, and ability to withstand high pressure, making them perfect for gas distribution systems.
2. How long do HDPE fittings last in gas pipeline systems?
HDPE fittings can last up to 50 years or more when properly installed and maintained, ensuring a long lifespan for gas pipelines.
3. Are HDPE fittings resistant to corrosion?
Yes, HDPE fittings are highly resistant to corrosion and chemical degradation, making them suitable for harsh environments where metal pipes would fail.
4. Can HDPE fittings be used for outdoor gas pipeline installations?
Yes, HDPE fittings are UV resistant and can be used for above-ground and outdoor gas pipeline installations without degrading under sunlight exposure.
5. How do HDPE fittings compare to PPR fittings for gas pipelines?
HDPE fittings are more suitable for gas pipelines due to their superior strength, chemical resistance, leak-free connections, and ability to withstand high pressure, while PPR fittings are better suited for water distribution systems.