IFAN factory 30+ years manufacture experience support color /size customization support free sample.Welcome to consult for catalog and free samples.This is our Facebook Website:www.facebook.com,Click to watch IFAN’s product video.Compared with Tomex products, our IFAN products from quality to price are your best choice, welcome to buy!
When it comes to building a reliable and sustainable water distribution system, HDPE fittings are a top choice due to their durability, flexibility, and ease of installation. Understanding how to properly install HDPE fittings is crucial to ensure the long-lasting performance of your piping system. This guide covers everything you need to know about HDPE fitting installation, from preparation to final inspection.
What Are HDPE Fittings?
HDPE fittings (High-Density Polyethylene fittings) are critical components in plumbing, water distribution, and industrial applications. Made from a high-density polyethylene material, these fittings are resistant to corrosion, chemicals, and extreme environmental conditions. They come in various shapes and sizes, including elbows, tees, couplings, and reducers, allowing for flexible installation across various systems.
Key Benefits of HDPE Fittings
- Durability: Resistant to corrosion, rust, and scaling, which extends the life of your system.
- Flexibility: HDPE fittings can withstand ground movements, temperature variations, and external stress without cracking or breaking.
- Leak-Proof: Provides tight, leak-free connections that minimize water loss.
- Cost-Effective: Long lifespan and low maintenance requirements make HDPE fittings a cost-efficient choice in the long run.
Now that we understand the importance of HDPE fittings, let’s explore the process of installing them correctly.
Preparation for Installing HDPE Fittings
1. Tools and Materials You Will Need
Before starting the installation process, ensure you have the necessary tools and materials:
- HDPE fittings (elbows, tees, reducers, etc.)
- HDPE pipes
- Pipe cutter or saw
- Fusion machine (for butt fusion or electrofusion welding)
- Pipe reaming tool
- Measuring tape
- Marking pen
- Protective gloves and safety gear
- Cleaning materials (cloth or brush)
Having all the required tools ensures a smooth installation process and prevents delays.
2. Planning the Layout
Before installing any fittings, plan the layout of your pipe system. Mark the location of where each HDPE fitting will be installed and measure the required pipe lengths accurately. This ensures precise connections and minimizes material waste.
Ensure that the installation area is clean and free of debris, as contaminants can interfere with the welding process and affect the fitting’s performance.
Steps for Installing HDPE Fittings
1. Cutting the Pipe
The first step in installing HDPE fittings is cutting the pipe to the required length. Use a pipe cutter or a fine-toothed saw to make a clean, straight cut. Any rough edges or burrs must be removed with a reaming tool to ensure a smooth, secure connection.
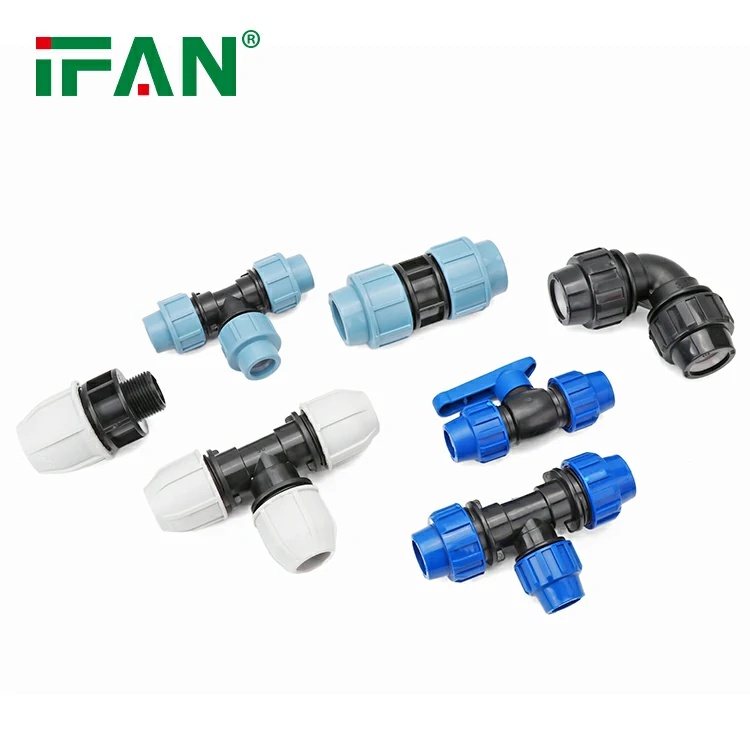
2. Cleaning the Pipe Ends
Clean the ends of the HDPE pipe thoroughly to remove any dirt, dust, or debris. This step is essential for a successful fusion process, as contaminants can compromise the strength of the weld. Use a clean cloth or brush to wipe the ends of the pipe before proceeding.
3. Aligning the Fittings
Once the pipe is ready, position the HDPE fitting onto the pipe. Ensure that the fitting aligns properly and fits snugly onto the pipe end. It’s crucial that the alignment is perfect to avoid leaks or weak joints. Misalignment can cause stress on the system and reduce its longevity.
4. Fusion Welding (Butt Fusion or Electrofusion)
There are two main methods for joining HDPE fittings to HDPE pipes: butt fusion and electrofusion.
Butt Fusion Welding
- Butt fusion is the most common method of joining HDPE fittings and pipes. This process involves heating the ends of the pipe and fitting using a fusion machine and then pressing them together to create a strong bond. The heating and pressure cause the plastic to melt and fuse, creating a seamless, leak-proof connection. Steps for Butt Fusion Welding:
- Place the pipe and fitting into the fusion machine.
- Heat both surfaces until they reach the correct temperature.
- Press the pipe and fitting together to form a secure weld.
- Hold the joint under pressure until it cools and solidifies.
Electrofusion Welding
- Electrofusion is typically used for smaller connections or where butt fusion is not practical. It involves using a fitting with built-in heating coils that, when electrified, melt the surfaces of the pipe and fitting to form a secure bond. Steps for Electrofusion Welding:
- Slide the electrofusion fitting onto the pipe.
- Connect the fitting’s terminals to an electrofusion welding machine.
- Start the welding process, which heats the fitting and pipe to form a secure connection.
- Wait for the fitting to cool and solidify.
5. Cooling and Testing the Joints
After welding, allow the joint to cool completely before handling it. This ensures that the connection solidifies properly and prevents any stress on the joint. Once the fitting is cool, conduct a pressure test to verify that the joint is secure and leak-proof. This step is crucial for confirming that the installation is successful.
6. Final Inspection
Perform a thorough inspection of the entire system to ensure all joints are properly installed and free from defects. Look for any visible cracks, misalignments, or potential weak points that may compromise the system’s integrity. It’s also a good idea to conduct a final pressure test to ensure the system is functioning correctly.
Tips for Successful HDPE Fitting Installation
- Precision is key: Measure and cut the pipes accurately to avoid wasting material and ensure the correct fit of HDPE fittings.
- Avoid contaminants: Keep the ends of the pipe clean during the installation process to ensure a strong, leak-proof weld.
- Proper heating: If using butt fusion welding, make sure the heating process is consistent and that both pipe and fitting are heated to the correct temperature.
- Follow manufacturer guidelines: Always refer to the manufacturer’s installation instructions for specific requirements and safety procedures.
Common Applications for HDPE Fittings
- Municipal water supply: HDPE fittings are widely used in municipal water distribution systems due to their durability and resistance to corrosion.
- Agricultural irrigation: Farmers rely on HDPE fittings for efficient and leak-proof irrigation systems.
- Industrial applications: Industries requiring chemical-resistant and high-pressure systems often use HDPE fittings to ensure reliable performance.
- Sewer and waste management: HDPE fittings are also suitable for wastewater treatment and sewer systems, where durability is essential.
Conclusion
Proper installation of HDPE fittings is vital to ensuring the success and longevity of your water distribution, irrigation, or industrial systems. By following the correct steps and using the appropriate welding methods, you can ensure that your system is leak-free, durable, and energy-efficient. Whether using butt fusion or electrofusion welding, understanding the installation process and adhering to best practices is essential for a reliable and sustainable infrastructure.
Frequently Asked Questions (FAQs)
1. What tools do I need to install HDPE fittings?
You will need a pipe cutter or saw, a fusion machine (for butt fusion or electrofusion), a reaming tool, measuring tape, and protective gloves.
2. Can I install HDPE fittings myself?
Yes, with the right tools and knowledge of the fusion welding process, you can install HDPE fittings yourself. It’s essential to follow all manufacturer instructions and safety guidelines.
3. What is the difference between butt fusion and electrofusion welding?
Butt fusion involves heating the pipe and fitting ends and pressing them together to form a strong bond, while electrofusion uses a fitting with built-in heating coils to fuse the pipe and fitting together.
4. How long does it take for HDPE fittings to cool after welding?
Cooling times vary depending on the size of the joint, but typically, it takes around 10-30 minutes for the joint to cool and solidify before handling.
5. Are HDPE fittings resistant to chemicals?
Yes, HDPE fittings are resistant to a wide range of chemicals, making them suitable for industrial and wastewater applications. However, always check compatibility with specific chemicals before installation.