IFAN factory 30+ years manufacture experience support color /size customization support free sample.Welcome to consult for catalog and free samples.This is our Facebook Website:www.facebook.com,Click to watch IFAN’s product video.Compared with Tomex products, our IFAN products from quality to price are your best choice, welcome to buy!
HDPE fittings (High-Density Polyethylene fittings) have become increasingly popular in various industries due to their remarkable durability and corrosion resistance. These properties make them an ideal choice for a wide range of applications, from water distribution systems to industrial pipelines. In this article, we will explore the factors contributing to the durability and corrosion resistance of HDPE fittings, how they compare to other materials, and why they are a smart investment for long-term infrastructure projects.
What are HDPE Fittings?
HDPE fittings are components made from high-density polyethylene, a type of thermoplastic polymer known for its robustness and versatility. These fittings are commonly used in plumbing, irrigation, and industrial applications, as well as for transporting water, gas, chemicals, and other substances. HDPE fittings come in various shapes and sizes, including elbows, tees, reducers, and flanges, and they can be joined using methods like butt fusion, electrofusion, or mechanical connections.
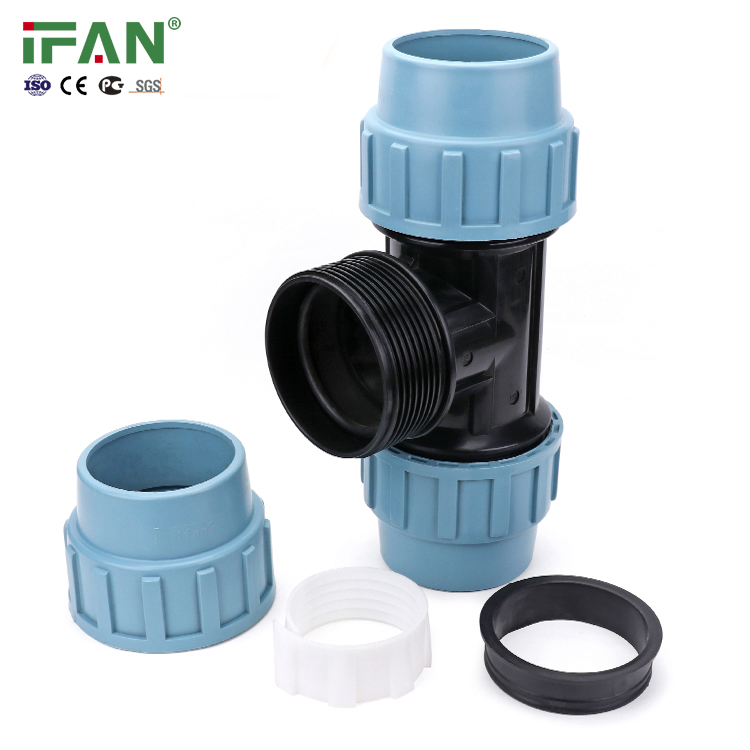
Durability of HDPE Fittings
Resistance to Physical Stress
One of the primary reasons HDPE fittings are chosen for critical applications is their exceptional durability under physical stress. HDPE fittings have high tensile strength, meaning they can withstand significant pressure without cracking or deforming. This makes them suitable for high-pressure water and gas systems where other materials like PVC or metal fittings might fail under stress.
HDPE fittings also exhibit high impact resistance. Whether subjected to freezing temperatures or physical blows, HDPE fittings are less likely to crack or shatter, ensuring that systems remain operational even under challenging conditions.
Long Lifespan
The lifespan of HDPE fittings is another key factor contributing to their popularity. When properly installed and maintained, HDPE fittings can last up to 50 years or more. This long lifespan is a result of the material’s resistance to various environmental factors, including temperature fluctuations, UV radiation, and physical wear.
Compared to traditional metal fittings, HDPE fittings do not corrode, rust, or degrade over time, making them a more reliable and cost-effective solution for long-term infrastructure projects.
Flexibility and Adaptability
Another remarkable feature of HDPE fittings is their flexibility. Unlike rigid materials like metal or PVC, HDPE is flexible enough to accommodate slight movements in the ground, such as settling or expansion due to temperature changes. This flexibility reduces the likelihood of joint failures, which are often a concern with more rigid materials. Additionally, HDPE fittings are resistant to cracking under stress, which makes them ideal for use in areas with seismic activity or shifting soil conditions.
Corrosion Resistance of HDPE Fittings
Resistance to Chemical Corrosion
HDPE fittings are known for their excellent resistance to chemical corrosion. Unlike metal pipes and fittings, which are prone to rust and corrosion when exposed to water, air, or certain chemicals, HDPE fittings remain unaffected by many acids, bases, and salts. This property makes HDPE fittings particularly useful in industrial applications where chemicals like hydrochloric acid or sulfuric acid may be present.
Furthermore, HDPE fittings are not susceptible to degradation from water or biological agents like algae, fungi, or bacteria, which can be a significant issue for other materials used in water distribution systems.
Resistance to UV Degradation
Exposure to ultraviolet (UV) radiation can weaken certain materials over time, leading to brittleness, cracking, and eventual failure. However, HDPE fittings are highly resistant to UV degradation, making them an excellent choice for outdoor applications. They can be used in direct sunlight without worrying about them losing their strength or integrity. In some cases, HDPE fittings can be coated with a UV-resistant layer for extra protection, ensuring they retain their structural properties even in the harshest environmental conditions.
Minimal Maintenance Requirements
One of the standout benefits of HDPE fittings is the minimal maintenance they require. Since HDPE fittings do not corrode or degrade over time, there is little need for routine inspection and maintenance compared to other materials. This translates into lower operational costs and reduced downtime, making them an economical option for large-scale infrastructure projects.
How HDPE Fittings Compare to Other Materials
HDPE vs. Metal Fittings
Metal fittings, such as those made from steel or copper, are commonly used in water and gas distribution systems. However, metal fittings are highly susceptible to corrosion, particularly in areas with high moisture levels or where the water is acidic. Over time, metal fittings can rust and deteriorate, leading to leaks, system failures, and costly repairs.
In contrast, HDPE fittings are completely resistant to corrosion, ensuring that they maintain their structural integrity over time. While metal fittings may offer higher tensile strength in some cases, HDPE fittings are much lighter and easier to install, reducing labor costs and improving overall efficiency.
HDPE vs. PVC Fittings
PVC (polyvinyl chloride) fittings are another popular alternative to HDPE fittings. PVC is also resistant to corrosion, but it lacks the flexibility and impact resistance of HDPE fittings. PVC fittings are prone to cracking under high pressure or physical stress, while HDPE fittings can handle more challenging conditions without failure.
In terms of chemical resistance, both HDPE fittings and PVC fittings are highly durable, but HDPE fittings have a broader range of resistance to chemicals, including those that might cause damage to PVC. HDPE fittings also tend to perform better in environments with extreme temperatures.
HDPE vs. CPVC Fittings
Chlorinated polyvinyl chloride (CPVC) fittings are often used in plumbing systems, particularly for hot water applications. While CPVC has better heat resistance than regular PVC, it is still more vulnerable to cracking and breakage under stress compared to HDPE fittings. Additionally, HDPE fittings offer better chemical resistance than CPVC, making them a more versatile option for industrial and chemical applications.
Why Choose HDPE Fittings for Your Projects?
Choosing HDPE fittings for your plumbing, gas, or industrial systems offers a variety of advantages, including:
- Long-lasting durability in high-stress conditions
- Excellent corrosion resistance to chemicals and water
- Flexibility to handle ground movement or temperature fluctuations
- Minimal maintenance requirements and lower operational costs
- Ease of installation with various joining methods
For these reasons, HDPE fittings are a reliable choice for both residential and industrial applications.
Frequently Asked Questions (FAQ)
- What are the main benefits of HDPE fittings?
- HDPE fittings are durable, resistant to corrosion, and flexible. They are also low-maintenance and have a long lifespan, making them ideal for water, gas, and chemical distribution systems.
- Can HDPE fittings be used for hot water applications?
- While HDPE fittings are excellent for cold and warm water applications, for high-temperature systems, consider using materials like CPVC, as HDPE has a maximum operating temperature limit of around 60°C to 80°C.
- Are HDPE fittings UV resistant?
- Yes, HDPE fittings are resistant to UV degradation, making them suitable for outdoor applications without the risk of becoming brittle or damaged by sunlight.
- How long do HDPE fittings last?
- When properly installed and maintained, HDPE fittings can last up to 50 years or more, offering long-term reliability for infrastructure projects.
- What is the best method for joining HDPE fittings?
- The most common methods for joining HDPE fittings are butt fusion, electrofusion, and mechanical connections. The choice of method depends on the application, pipe size, and available tools.