IFAN factory 30+ years manufacture experience support color /size customization support free sample.Welcome to consult for catalog and free samples.This is our Facebook Website:www.facebook.com,Click to watch IFAN’s product video.Compared with Tomex products, our IFAN products from quality to price are your best choice, welcome to buy!
Installing HDPE (High-Density Polyethylene) fittings properly is crucial to ensure the longevity and efficiency of your piping systems. HDPE fittings are known for their durability, resistance to corrosion, and flexibility, making them a top choice for a wide range of applications, from plumbing and irrigation to industrial piping systems. However, improper installation can lead to leaks, system failures, and expensive repairs. In this article, we’ll walk through the common mistakes to avoid when installing HDPE fittings, so you can ensure a smooth and effective installation process.
1. Ignoring Manufacturer’s Guidelines
One of the most common mistakes when installing HDPE fittings is disregarding the manufacturer’s installation guidelines. Every HDPE fitting comes with specific instructions for installation, including guidelines on appropriate welding methods, temperatures, and fitting compatibility. Ignoring these recommendations can result in weak connections that may leak or fail over time.
Tip: Always read and follow the manufacturer’s instructions for installation to ensure a secure and durable connection. Adhering to guidelines for HDPE fittings ensures the system is safe, effective, and compliant with local standards.
2. Using the Wrong Welding Method
Welding is one of the most common methods used to join HDPE pipes and fittings. However, it is essential to use the correct welding technique to ensure a strong, leak-proof connection. There are different welding methods for HDPE fittings, such as butt fusion welding and electrofusion welding. Using the wrong welding method or improperly executing it can compromise the integrity of the system.
Tip: Choose the appropriate welding technique based on the type of fitting and the requirements of your specific application. Butt fusion welding works best for larger pipes, while electrofusion welding is ideal for smaller diameter pipes and more complex installations.
3. Incorrect Pipe Alignment
Proper alignment of HDPE pipes and fittings is critical to ensure the system operates correctly. Misalignment of pipes during installation can result in stress on the joints, causing potential failure. Additionally, incorrect alignment can lead to uneven flow rates and increased wear on the fittings.
Tip: Ensure that the pipes and fittings are correctly aligned before welding or connecting. Using alignment tools and laser equipment can help maintain precision and avoid unnecessary stress on the system.
4. Failing to Clean the Surfaces Before Welding
Before welding HDPE fittings, it is essential to clean both the pipe and fitting surfaces. Any dirt, grease, or debris left on the surfaces can prevent a proper fusion, leading to weak joints that are prone to leaks. This mistake is often overlooked but can significantly reduce the strength and longevity of the HDPE system.
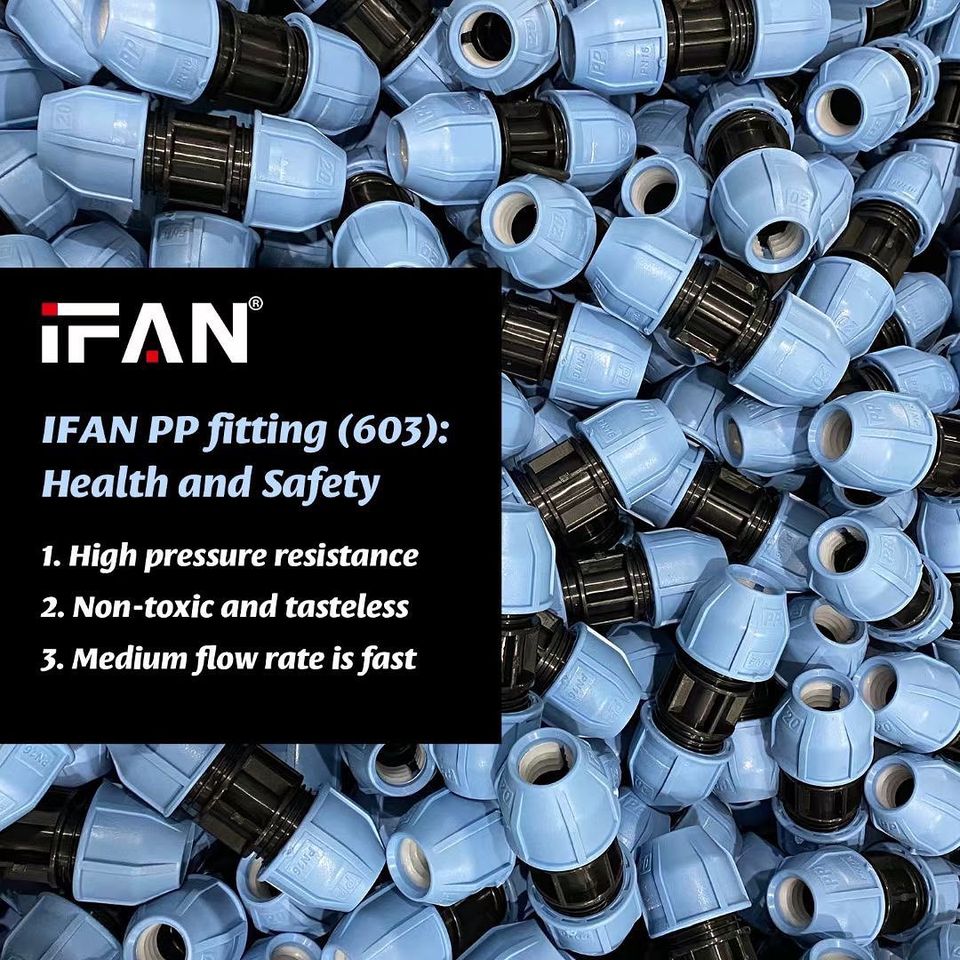
Tip: Always clean the surfaces of the pipes and fittings thoroughly before beginning the welding process. Use a clean cloth and suitable cleaning agent to remove any contaminants that could interfere with the fusion process.
5. Using Incompatible Fittings
HDPE fittings come in various sizes, shapes, and designs, and it’s essential to ensure that the fittings you use are compatible with the pipes you’re working with. Using incompatible fittings, such as mismatched sizes or incompatible pressure ratings, can result in poor connections and system failure.
Tip: Double-check the size, pressure rating, and material compatibility of the fittings before installation. Always verify that the fittings match the specifications of the pipes to ensure a secure and long-lasting connection.
6. Overheating or Underheating During Welding
HDPE fittings rely on heat to create a strong bond between pipes and fittings. However, overheating or underheating the materials can weaken the weld and compromise the integrity of the system. Overheating can cause the material to become too soft, while underheating may result in an incomplete fusion.
Tip: Use a temperature-controlled welding machine to ensure that the pipes and fittings are heated to the proper temperature for fusion. Follow the manufacturer’s recommended temperature guidelines to avoid damage to the materials.
7. Not Allowing Enough Cooling Time
Once the HDPE fittings have been welded, it is essential to allow them sufficient cooling time before handling or testing. Rushing this process can weaken the bond, resulting in leaks and failures in the system. Proper cooling ensures that the fusion is fully set and stable before the system is put into use.
Tip: Allow adequate time for the welded joints to cool completely before applying pressure or testing the system. Follow the recommended cooling time as outlined in the manufacturer’s instructions to ensure the fitting’s longevity and strength.
8. Not Using the Right Tools
Using improper tools during the installation process can lead to mistakes and complications. For example, using a manual pipe cutter instead of a proper pipe saw or cutting tool may result in uneven cuts that affect the fit of the HDPE fittings. Additionally, using the wrong welding equipment or pressure testing tools can negatively affect the system’s performance.
Tip: Ensure that you have the proper tools and equipment for the installation. Invest in high-quality pipe cutters, welders, and pressure testing equipment that are compatible with HDPE fittings.
9. Neglecting to Test the System After Installation
Once the HDPE fittings are installed, many installers neglect to perform a thorough test of the system. Without proper pressure testing and visual inspection, leaks or faults may go undetected, leading to costly repairs and potential system failures down the line.
Tip: Always conduct a pressure test after installation to ensure there are no leaks in the system. Visually inspect the fittings for any signs of stress or damage, and verify that the system is functioning correctly before use.
10. Using Old or Damaged Fittings
HDPE fittings are designed to last for decades, but using damaged or old fittings can cause issues during installation. Cracks, wear, or aging can compromise the fitting’s ability to create a secure seal, increasing the risk of leaks.
Tip: Inspect all fittings before installation to ensure that they are free from defects and damage. If any fittings appear worn or cracked, replace them with new ones to avoid future problems.
Conclusion
Proper installation of HDPE fittings is essential for ensuring the efficiency and longevity of your piping systems. Avoiding the common mistakes listed in this article will help you achieve a secure, leak-free, and durable connection. By following the manufacturer’s guidelines, using the right tools and techniques, and testing the system thoroughly after installation, you can ensure that your HDPE fittings perform optimally for years to come.
Frequently Asked Questions (FAQs)
- What are the benefits of using HDPE fittings?
- HDPE fittings are durable, corrosion-resistant, flexible, and cost-effective. They are ideal for a variety of applications, including plumbing, irrigation, and industrial piping systems.
- How do I choose the right welding method for HDPE fittings?
- The welding method depends on the type of installation. Butt fusion welding is suitable for larger pipes, while electrofusion welding is often used for smaller diameter pipes and more complex configurations.
- What tools do I need for installing HDPE fittings?
- Essential tools include a pipe cutter, welding machine, alignment tools, and pressure testing equipment. Using the right tools ensures a proper and efficient installation process.
- How long do HDPE fittings last?
- HDPE fittings are highly durable and can last for decades, often exceeding 50 years in proper conditions. They are resistant to corrosion and harsh environmental factors.
- Can I use HDPE fittings in high-pressure systems?
- Yes, HDPE fittings are suitable for high-pressure systems, but it’s crucial to choose fittings that are rated for the required pressure and ensure proper welding and installation techniques are used.