IFAN factory 30+ years manufacture experience support color /size customization support free sample.Welcome to consult for catalog and free samples.This is our Facebook Website:www.facebook.com,Click to watch IFAN’s product video.Compared with Tomex products, our IFAN products from quality to price are your best choice, welcome to buy!
PPR fittings (Polypropylene Random Copolymer) are becoming increasingly popular in plumbing and piping systems due to their durability, cost-effectiveness, and ease of installation. However, improper installation can lead to leaks, system failures, and expensive repairs. To help you avoid common installation errors and ensure your PPR piping system functions optimally, we have outlined the top installation mistakes to avoid with PPR fittings.
1. Not Using the Proper Fusion Welding Equipment
One of the most common installation mistakes when working with PPR fittings is not using the proper fusion welding equipment. PPR fittings require a fusion welding process to create a secure and leak-proof connection between the pipes and fittings. This process involves heating both the pipe and the fitting to a specific temperature, then joining them under pressure.
Why It’s Important:
Using the wrong equipment, or not heating the pipe and fitting correctly, can result in weak joints that may leak over time. It is crucial to use the right fusion machine with proper settings for your specific PPR pipes and fittings. Additionally, using old or damaged welding equipment can lead to inconsistent results, undermining the integrity of your plumbing system.
How to Avoid It:
Always ensure you use a high-quality fusion welding machine and follow the manufacturer’s instructions for temperature and timing settings. Verify that the fusion machine is in good condition before starting any installation.
2. Incorrectly Cutting PPR Pipes
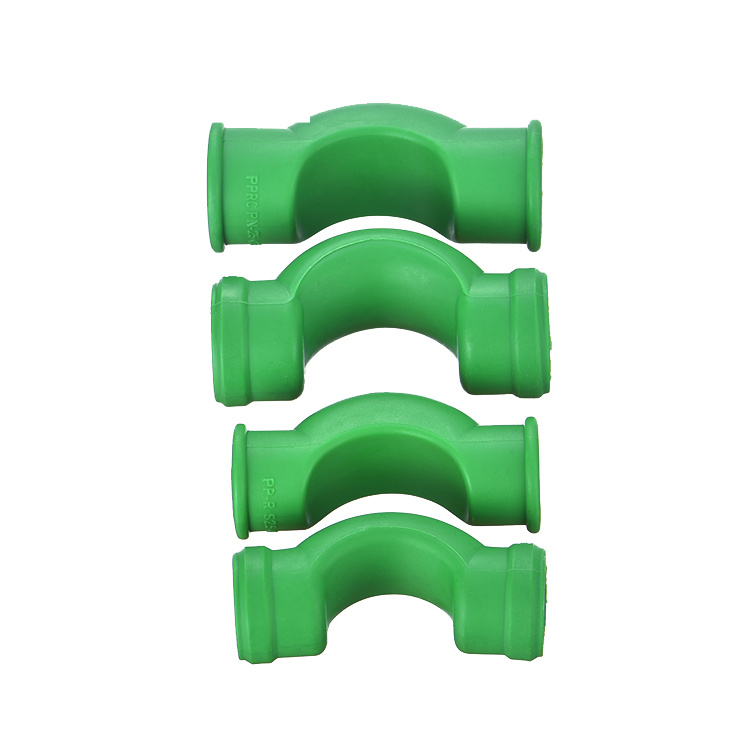
Cutting PPR pipes may seem simple, but improper cutting can lead to issues during the installation process. Using the wrong type of cutter, or cutting the pipe too short or unevenly, can make it difficult to ensure a tight seal during the fusion welding process.
Why It’s Important:
If the ends of the PPR pipe are not cut squarely or uniformly, the fusion process will not create a reliable bond. This can result in leaks and compromised system performance.
How to Avoid It:
Use a pipe cutter specifically designed for PPR pipes to make a clean and accurate cut. Ensure that the cut is perfectly straight, and that the pipe is the correct length before proceeding with the installation.
3. Not Cleaning the Pipe and Fitting Before Welding
Before joining PPR fittings to pipes, it is essential to thoroughly clean the surfaces. This step is often overlooked, but failure to do so can lead to poor fusion, leaks, and decreased system performance.
Why It’s Important:
Dirt, dust, or debris on the pipe or fitting surfaces can prevent a solid fusion bond from forming. Even a small amount of contamination can compromise the integrity of the joint and cause future problems.
How to Avoid It:
Clean the ends of both the pipe and fitting with a clean cloth or an appropriate solvent before starting the fusion process. Ensure the surfaces are completely dry before proceeding.
4. Overheating or Underheating During Fusion Welding
Fusion welding of PPR fittings requires careful control of temperature. Overheating or underheating can both cause problems. Overheating can cause the material to degrade, while underheating will result in insufficient bonding, leading to weak joints.
Why It’s Important:
If the pipe and fitting are not heated to the correct temperature, the fusion process will not create a reliable bond. Overheated materials can weaken the pipe, while underheated pipes and fittings may not form a secure joint, leading to future leaks.
How to Avoid It:
Ensure the welding machine is set to the manufacturer-recommended temperature. Monitor the fusion process closely to avoid overheating or underheating. Typically, a temperature range of 250°C to 270°C (482°F to 518°F) is ideal for PPR fittings, but always refer to the manufacturer’s instructions for precise settings.
5. Inadequate Cooling Time After Fusion Welding
Once you have completed the fusion welding of PPR fittings, it’s important to allow enough cooling time before applying pressure to the joint. Rushing the cooling process can result in weak or improperly fused connections.
Why It’s Important:
Prematurely applying pressure to a newly fused joint before it has cooled can cause the joint to fail. The cooling time allows the materials to solidify and form a strong, leak-proof bond.
How to Avoid It:
Allow sufficient time for the pipe and fitting to cool naturally before subjecting them to any pressure. The cooling time will depend on the size of the pipe and the ambient temperature, but generally, it is recommended to wait at least 5 minutes before moving the joint.
6. Using PPR Fittings in Inappropriate Applications
While PPR fittings are versatile, they are not suitable for all plumbing applications. Using PPR fittings in areas where they are not recommended can result in system failures and costly repairs.
Why It’s Important:
PPR fittings are designed to handle a wide range of temperatures and pressures, but they should not be used for gas lines, outdoor installations in extreme temperatures, or applications where chemical exposure is high.
How to Avoid It:
Make sure to use PPR fittings only in applications that are within the temperature and pressure limits recommended by the manufacturer. For gas lines, use fittings specifically designed for gas, and for outdoor applications, ensure proper insulation is used to protect the system from UV exposure.
7. Not Testing the System After Installation
After installing PPR fittings, some installers forget to perform a pressure test to check for leaks. Failing to test the system before putting it into operation can lead to undetected leaks that might cause serious damage over time.
Why It’s Important:
Testing the system ensures that all connections are properly welded and that no leaks are present. It’s much easier to address small leaks immediately than to wait for them to become bigger problems later.
How to Avoid It:
After installation, perform a thorough pressure test of the entire plumbing system to identify any leaks. This should be done using the recommended pressure values for your PPR system.
8. Using the Wrong Type of PPR Fittings
Not all PPR fittings are created equal, and using the wrong type for your specific needs can lead to failures in the system. PPR fittings come in a variety of types, each designed for specific uses such as hot water systems, cold water systems, or specialized applications like underfloor heating.
Why It’s Important:
Using the wrong fittings can compromise the integrity of the plumbing system. For example, using fittings designed for cold water in a hot water system can result in deformation, leakage, or pipe failure.
How to Avoid It:
Ensure you select the correct type of PPR fittings based on the specific requirements of your plumbing system. Always verify the temperature and pressure rating of the fittings before installation.
9. Neglecting to Insulate Pipes in Certain Environments
While PPR fittings are highly durable, certain environmental conditions can cause the pipes to degrade over time if not properly insulated. This is particularly important in areas with extreme temperatures.
Why It’s Important:
Extreme cold or heat can cause PPR pipes to become brittle or expand, leading to cracks or joint failures. Proper insulation helps maintain the integrity of the system and extends its lifespan.
How to Avoid It:
Ensure that PPR pipes are adequately insulated in areas prone to temperature extremes, such as outdoor installations or in cold climates.
FAQs About PPR Fittings Installation
- What are the temperature limits for PPR fittings?
- PPR fittings can withstand temperatures up to 95°C (203°F) for hot water applications, making them suitable for both cold and hot water systems.
- Can I install PPR fittings myself?
- Yes, PPR fittings are relatively easy to install, especially with fusion welding machines, but it’s crucial to follow proper installation techniques to avoid common mistakes.
- How long does it take for PPR fittings to cool after fusion welding?
- Typically, 5 to 10 minutes is sufficient for the cooling process, but it depends on the size of the pipe and the ambient temperature.
- Can PPR fittings be used for gas lines?
- No, PPR fittings are not suitable for gas lines. They are intended for water and heating systems only.
- Do I need to test the system after installing PPR fittings?
- Yes, it’s essential to perform a pressure test after installation to check for leaks and ensure all joints are securely fused.
By avoiding these common installation mistakes, you can ensure that your PPR fittings will perform reliably for many years to come, minimizing maintenance costs and ensuring optimal system efficiency.