IFAN factory 30+ years manufacture experience support color /size customization support free sample.Welcome to consult for catalog and free samples.This is our Facebook Website:www.facebook.com,Click to watch IFAN’s product video.Compared with Tomex products, our IFAN products from quality to price are your best choice, welcome to buy!
In recent years, PPR fittings have become increasingly popular in industrial applications due to their excellent durability, corrosion resistance, and cost-effectiveness. Made from polypropylene random copolymer (PPR), these fittings offer numerous advantages that make them ideal for industrial environments where reliability and performance are paramount. This article delves into the features, benefits, and applications of PPR fittings in industrial settings, ensuring that you make an informed decision when selecting materials for your systems.
What Are PPR Fittings?
PPR fittings are components made from polypropylene random copolymer, a durable thermoplastic material used for piping systems. These fittings are widely used in both residential and industrial applications due to their robustness, resistance to corrosion, and ease of installation. Common forms of PPR fittings include elbows, tees, couplings, reducers, ball valves, and flanges, which are all designed to connect, control, and modify the flow of liquids in industrial piping systems.
PPR fittings are compatible with PPR pipes, offering a complete piping solution for various systems, including hot and cold water systems, chemical transport systems, and industrial fluid pipelines.
Key Advantages of PPR Fittings for Industrial Applications
1. Durability and Longevity
One of the primary reasons PPR fittings are favored in industrial settings is their remarkable durability. PPR fittings are resistant to a wide range of factors that can typically damage other materials, including chemicals, high temperatures, and high-pressure systems. These fittings can withstand temperatures up to 95°C (203°F) and pressures that are common in industrial applications. When installed properly, PPR fittings can last for decades without the need for significant maintenance.
2. Corrosion Resistance
Unlike metal fittings, which are prone to corrosion over time, PPR fittings are highly resistant to the effects of both rust and corrosion. This is especially important in industrial applications where exposure to harsh chemicals and water can lead to the deterioration of metal parts. The inherent corrosion resistance of PPR fittings ensures a longer lifespan and reduced maintenance costs, making them an economical choice for industrial piping systems.
3. Chemical Resistance
Industrial environments often require piping systems that can handle a variety of chemicals. PPR fittings are resistant to most chemicals, making them an excellent choice for chemical transportation in industries such as manufacturing, food processing, and pharmaceuticals. The ability of PPR fittings to resist the harmful effects of various chemicals reduces the likelihood of leaks, damage, or system failure, ensuring the safety and efficiency of the operation.
4. Cost-Effectiveness
While PPR fittings may have a higher upfront cost compared to some other plastic materials, their long lifespan and low maintenance requirements make them a highly cost-effective solution in the long run. The absence of corrosion and scaling issues means that PPR fittings require minimal repairs or replacements, leading to significant savings over time.
5. Ease of Installation
The installation of PPR fittings is relatively simple compared to other materials, such as metal or PVC. These fittings can be welded together using heat fusion, which creates strong, leak-free joints. This process not only reduces the time and effort required for installation but also minimizes the risk of leaks or other installation-related issues. As a result, PPR fittings help streamline the construction and maintenance of industrial piping systems.
6. Lightweight and Flexible
Despite their durability, PPR fittings are lightweight, making them easy to handle and install. Their flexibility allows for easier transportation, assembly, and installation, even in tight spaces. This is especially advantageous in industrial settings, where ease of movement and quick setup are critical factors.
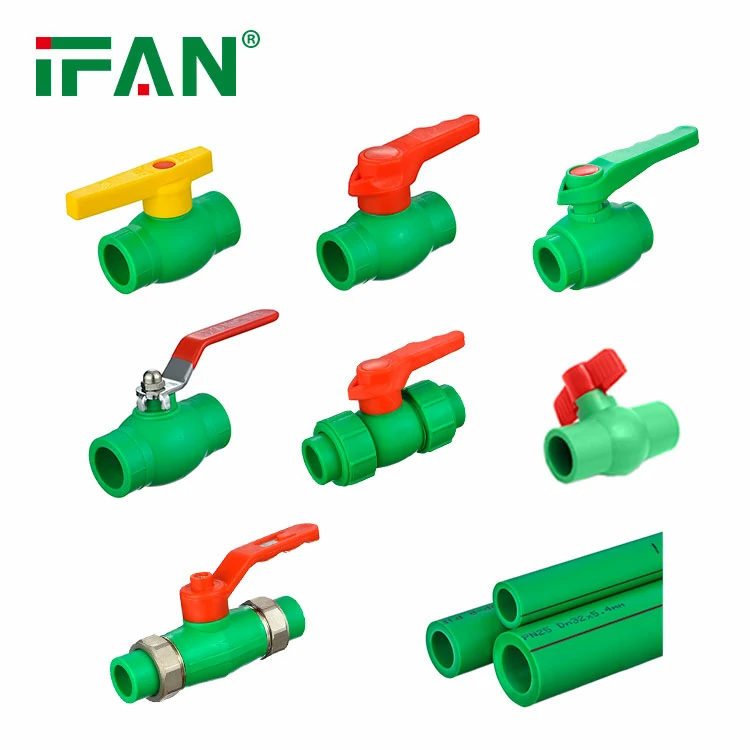
7. Environmentally Friendly
PPR fittings are recyclable, making them an eco-friendly choice for industries looking to minimize their environmental impact. The ability to recycle PPR fittings reduces waste and promotes sustainability, which is becoming increasingly important for businesses focused on environmental responsibility.
Industrial Applications of PPR Fittings
1. Water and Wastewater Systems
PPR fittings are widely used in industrial water and wastewater systems due to their resistance to corrosion and chemicals. They are commonly found in applications such as cooling systems, water treatment plants, and industrial piping networks. The ability of PPR fittings to handle both hot and cold water systems ensures that they can be employed in a wide range of environments, from power plants to manufacturing facilities.
2. Chemical Processing Systems
In industries such as chemicals, pharmaceuticals, and food processing, PPR fittings are used to transport chemicals and liquids through pipes. Their resistance to chemical degradation makes them ideal for environments where aggressive substances are present. These fittings are used in the transportation of acids, alkalis, solvents, and other chemicals that may cause traditional metals to corrode or degrade.
3. HVAC Systems
In industrial HVAC (Heating, Ventilation, and Air Conditioning) systems, PPR fittings are often used for the installation of piping systems that carry refrigerants and hot or cold water. These systems require reliable, long-lasting materials that can withstand temperature fluctuations and high-pressure conditions, making PPR fittings an excellent choice for HVAC applications.
4. Food and Beverage Industry
In the food and beverage industry, the safe and efficient transportation of liquids is essential. PPR fittings are commonly used for piping systems in breweries, dairies, and soft drink manufacturing plants due to their resistance to contamination and the ability to handle both hot and cold liquids. The non-corrosive nature of PPR fittings ensures that there is no risk of contamination during the processing of food and beverages.
5. Pharmaceutical Manufacturing
The pharmaceutical industry requires highly sterile and reliable piping systems for transporting liquids and chemicals. PPR fittings are used in pharmaceutical plants to transport water, chemicals, and other substances that require sterile conditions. The non-reactive and corrosion-resistant properties of PPR fittings help ensure the integrity of the system, maintaining product quality and preventing contamination.
How to Choose the Right PPR Fittings for Your Industrial Needs
When selecting PPR fittings for industrial applications, consider the following factors to ensure optimal performance:
- Temperature and Pressure Ratings: Ensure that the PPR fittings you choose are rated to handle the temperature and pressure conditions of your specific application. Industrial systems often operate under high-pressure and high-temperature conditions, so it’s essential to select fittings that can withstand these stresses.
- Chemical Compatibility: Depending on the chemicals being transported, ensure that the PPR fittings are compatible with the substances in question. Some chemicals can degrade certain types of plastics, so it’s important to verify compatibility before installation.
- Size and Configuration: Choose the correct size and configuration of PPR fittings to ensure that they match the requirements of your piping system. Proper sizing ensures efficient flow and prevents issues such as blockages or pressure drops.
- Installation Environment: Consider factors such as exposure to UV radiation, temperature fluctuations, and physical stress in the environment where the PPR fittings will be installed. If the fittings will be exposed to sunlight or harsh environmental conditions, UV-resistant coatings may be required.
Common Issues with PPR Fittings in Industrial Applications
While PPR fittings are generally reliable, a few issues can arise if not properly installed or maintained:
- Improper Welding: Incorrect welding during installation can result in weak joints, leading to leaks or system failure. Ensure that the correct welding temperature and procedure are followed during installation.
- Over-tightening: Over-tightening of threaded PPR fittings can cause stress cracks and leaks. Always follow the manufacturer’s recommended torque specifications when tightening fittings.
- UV Degradation: PPR fittings can degrade when exposed to UV radiation over extended periods. For outdoor or exposed installations, consider using UV-resistant fittings or coatings to prevent degradation.
Frequently Asked Questions (FAQs)
1. What are PPR fittings made of?
PPR fittings are made from polypropylene random copolymer (PPR), a thermoplastic material known for its resistance to heat, chemicals, and corrosion.
2. Can PPR fittings be used for hot water?
Yes, PPR fittings are designed to withstand temperatures up to 95°C (203°F), making them suitable for both hot and cold water applications.
3. Are PPR fittings safe for chemical transport?
Yes, PPR fittings offer excellent resistance to most chemicals, making them a safe choice for industrial chemical transport systems.
4. How long do PPR fittings last?
With proper installation and maintenance, PPR fittings can last 50 years or more, making them a long-term solution for industrial piping systems.
5. Can PPR fittings be recycled?
Yes, PPR fittings are made from recyclable materials, making them an eco-friendly option for industrial applications.
By understanding the features and applications of PPR fittings, industrial businesses can make informed decisions that ensure the longevity, safety, and efficiency of their systems. Whether you’re dealing with water systems, chemical processing, or HVAC, PPR fittings are a reliable and cost-effective solution for your industrial needs.