IFAN factory 30+ years manufacture experience support color /size customization support free sample.Welcome to consult for catalog and free samples.This is our Facebook Website:www.facebook.com,Click to watch IFAN’s product video.Compared with Tomex products, our IFAN products from quality to price are your best choice, welcome to buy!
In the world of plumbing and piping systems, choosing the right type of fittings is crucial for ensuring the longevity, reliability, and cost-effectiveness of infrastructure. Among the most commonly used materials for fittings are HDPE fittings (High-Density Polyethylene) and traditional metal fittings (such as copper, steel, and brass). Both materials offer distinct advantages and limitations, making it important to compare them based on key factors like durability, cost, and installation requirements. This article will explore how HDPE fittings stack up against metal fittings, with a focus on durability and cost factors.
What Are HDPE Fittings?
HDPE fittings are components made from High-Density Polyethylene, a thermoplastic polymer known for its strength, flexibility, and resistance to corrosion. These fittings are widely used in various industries, such as water distribution, sewage systems, industrial piping, and gas transport. They are commonly available in shapes like elbows, tees, couplings, reducers, and flanges.
Unlike metal fittings, HDPE fittings do not rust, corrode, or scale over time, making them ideal for challenging environments. They are lightweight, easy to install, and have a long service life, making them an attractive option for many infrastructure projects.
What Are Metal Fittings?
Metal fittings are components made from metals like steel, copper, and brass, and they are traditionally used in plumbing, industrial systems, and water distribution networks. Metal fittings have been the go-to solution for decades, known for their strength and high-pressure resistance. However, over time, metals can suffer from corrosion, scaling, and wear, which can impact their performance and longevity.
Common types of metal fittings include steel fittings, copper fittings, and brass fittings, each offering its own set of benefits and limitations.
Durability: HDPE Fittings vs. Metal Fittings
1. Corrosion Resistance
HDPE fittings stand out in terms of corrosion resistance. Unlike metal fittings, which are prone to rust and corrosion over time (especially in high-moisture or acidic environments), HDPE fittings are naturally resistant to corrosion. This makes them ideal for underground installations, where they can be exposed to soil, moisture, and other corrosive elements.
For example, steel fittings are highly susceptible to rusting and can deteriorate significantly over time if exposed to moisture, while copper fittings are vulnerable to corrosion caused by acidic or alkaline water. In contrast, HDPE fittings do not rust, ensuring that the integrity of the piping system is maintained for a much longer period.
2. Resistance to Environmental Stress
HDPE fittings are also resistant to environmental stress, such as UV radiation, temperature fluctuations, and ground movement. While metals can become brittle or degrade when exposed to UV light (e.g., in outdoor applications), HDPE fittings remain flexible and strong under similar conditions. They are ideal for both underground and above-ground applications, where environmental factors may cause metal fittings to crack or weaken.
On the other hand, metal fittings, particularly steel and brass, are more susceptible to damage from environmental stress, especially in extreme climates. Exposure to UV rays or freezing temperatures can cause cracks and leaks in metal pipes and fittings, leading to costly repairs and replacements.
3. Impact Resistance
In terms of impact resistance, HDPE fittings have the edge over metal fittings. HDPE is a highly flexible material, which allows it to absorb shock and impact without cracking or breaking. This makes HDPE fittings a great choice for installations where mechanical stress or physical impact is a concern.
While metal fittings are stronger in terms of load-bearing capacity, they are more prone to cracking under impact, especially at the joints or bends. In contrast, HDPE fittings can withstand much more physical stress without damage.
Cost Factors: HDPE Fittings vs. Metal Fittings
1. Initial Material Costs
When it comes to initial material costs, metal fittings tend to be more expensive than HDPE fittings. Materials like copper, brass, and stainless steel can be costly, especially in high-demand markets. For example, copper fittings are known for their high price, often making them less cost-effective for large-scale projects.
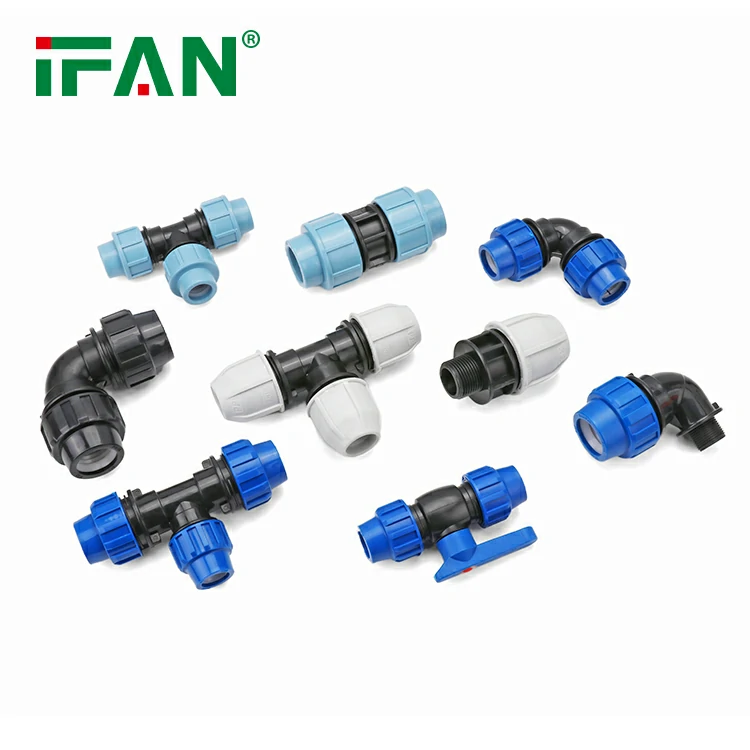
HDPE fittings, on the other hand, are relatively affordable. Although they might have a slightly higher upfront cost compared to some low-cost metals like galvanized steel, they are still cheaper than more expensive metals like copper and brass. For large projects requiring a significant number of fittings, HDPE fittings offer a more budget-friendly alternative.
2. Installation Costs
The installation costs of HDPE fittings are generally lower than those of metal fittings. HDPE fittings are lightweight and easy to handle, reducing labor costs and the need for heavy machinery during installation. The fusion method used to join HDPE fittings (such as heat fusion) creates a seamless bond that is quick and simple to perform.
In contrast, metal fittings require more complex installation processes. Copper fittings, for example, often require soldering, while steel fittings may need welding or threading. These processes are more time-consuming and require specialized tools and skills, which can increase installation costs significantly.
3. Maintenance and Replacement Costs
While metal fittings may have a lower initial cost, their long-term maintenance and replacement costs tend to be higher due to their susceptibility to corrosion and wear. Over time, metal fittings may need frequent repairs, replacements, or refinishing, particularly if they are used in corrosive or harsh environments.
HDPE fittings, due to their superior durability and resistance to corrosion, require significantly less maintenance. They are designed to last for decades without needing repairs or replacements, making them a more cost-effective option in the long run.
Conclusion: Which is Better for Your Project?
When comparing HDPE fittings with metal fittings, it becomes clear that each material has its own strengths and weaknesses. HDPE fittings are highly durable, cost-effective, and resistant to environmental stress, making them an excellent choice for sustainable infrastructure projects. They offer long-term savings through reduced maintenance and replacement costs.
Metal fittings, on the other hand, may still be suitable for certain applications where high strength and pressure resistance are required. However, their susceptibility to corrosion, environmental damage, and higher installation and maintenance costs can make them less ideal for many modern construction projects.
Ultimately, the choice between HDPE fittings and metal fittings depends on the specific needs of the project. For cost-effective, low-maintenance, and sustainable solutions, HDPE fittings are the clear winner. However, for high-pressure, heavy-duty applications, metal fittings may still have a role to play.
Frequently Asked Questions (FAQs)
1. What are HDPE fittings made of?
HDPE fittings are made from High-Density Polyethylene, a strong, flexible thermoplastic material that is resistant to corrosion, chemicals, and environmental stress.
2. Are HDPE fittings more durable than metal fittings?
Yes, HDPE fittings are more durable in many ways, particularly in terms of corrosion resistance, environmental stress resistance, and impact resistance. They generally have a longer lifespan than metal fittings.
3. Are HDPE fittings more cost-effective than metal fittings?
HDPE fittings are generally more affordable than metal fittings, both in terms of material cost and installation expenses. They also have lower long-term maintenance and replacement costs.
4. Can HDPE fittings be used in high-pressure systems?
Yes, HDPE fittings are suitable for use in high-pressure systems, especially in water distribution and industrial applications, provided they are properly rated for the specific pressure requirements.
5. How are HDPE fittings joined?
HDPE fittings are typically joined using heat fusion, which creates a seamless, leak-proof connection between the fittings and pipes. This method is fast, reliable, and requires minimal tools and labor.