IFAN factory 30+ years manufacture experience support color /size customization support free sample.Welcome to consult for catalog and free samples.This is our Facebook Website:www.facebook.com,Click to watch IFAN’s product video.Compared with Tomex products, our IFAN products from quality to price are your best choice, welcome to buy!
High-Density Polyethylene (HDPE) fittings are an essential part of modern plumbing, water, and gas distribution systems. Known for their strength, flexibility, and resistance to chemicals, HDPE fittings are widely used in various industries, including construction, agriculture, and wastewater management. This article will provide an in-depth look at the HDPE fitting manufacturing process, highlighting the steps involved, the materials used, and the advantages of using HDPE in piping systems. Whether you’re a contractor, engineer, or DIY enthusiast, understanding how HDPE fittings are made will help you make informed decisions when selecting piping components for your projects.
What Are HDPE Fittings?
HDPE fittings are parts used to connect, redirect, or terminate pipes in plumbing systems. Made from HDPE plastic, these fittings offer excellent durability, resistance to corrosion, and the ability to withstand extreme conditions. HDPE fittings come in various forms, including elbows, tees, couplings, reducers, and flanges, each designed for specific applications. Due to their resistance to rust, corrosion, and chemical degradation, HDPE fittings are preferred in industries like water treatment, oil and gas, and agriculture.
The Manufacturing Process of HDPE Fittings
The process of manufacturing HDPE fittings involves several critical steps, each designed to ensure that the final product meets stringent quality standards. Below is an overview of the typical manufacturing process.
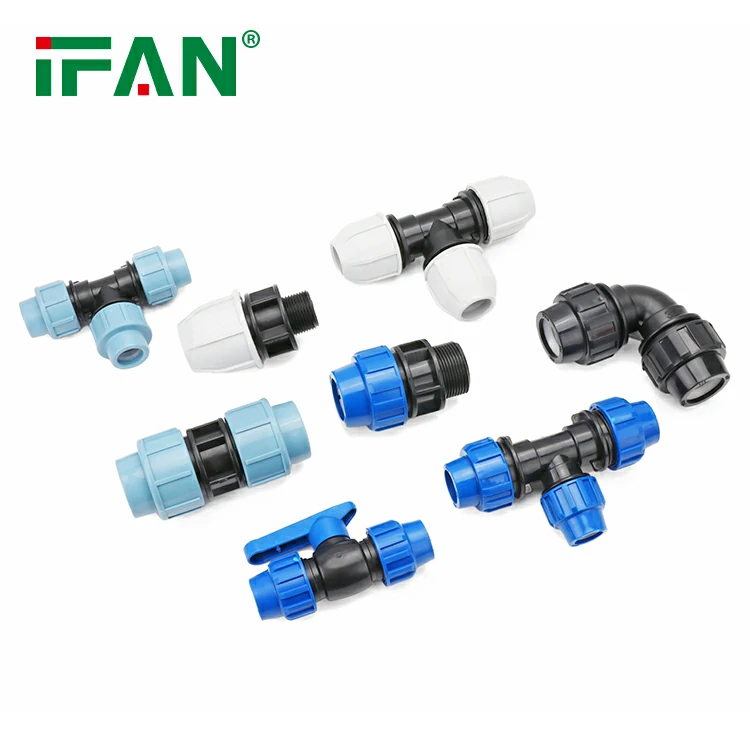
1. Material Selection
The first step in the manufacturing process is selecting the right grade of HDPE resin. HDPE is a thermoplastic polymer, which means it can be molded into various shapes when heated. The resin used for manufacturing HDPE fittings is specifically chosen for its strength, chemical resistance, and flexibility. The quality of the HDPE resin is crucial because it directly impacts the durability and performance of the fittings.
2. Injection Molding or Extrusion
Once the material is selected, the next step is to shape the HDPE fittings using either the injection molding or extrusion process. Both processes are designed to create different types of fittings, depending on their application.
- Injection Molding: This process involves melting the HDPE resin and injecting it into molds under high pressure. Injection molding is used to produce small to medium-sized fittings like elbows, tees, and adapters. The molds are carefully crafted to the precise specifications, ensuring that each fitting is uniform in size and shape.
- Extrusion: For larger fittings, such as pipes and flanges, the extrusion process is used. In this method, the HDPE resin is melted and forced through a mold to form the desired shape. Extrusion is commonly used for long, continuous fittings or those with a simple shape.
Both methods ensure that the HDPE fittings are strong, consistent, and meet the required standards.
3. Cooling and Solidification
After molding or extrusion, the fittings are cooled to solidify the material. This step is crucial, as it ensures the fittings retain their shape and strength. The cooling process can be done using air cooling or water baths, depending on the size and complexity of the fittings.
4. Cutting and Shaping
Once the HDPE fittings have cooled and solidified, they are cut to the appropriate length or size. Some fittings may need to be further shaped or resized to fit specific applications. For instance, flanges may be trimmed, and ends may be bevelled to ensure proper sealing when connected to other pipes.
5. Fitting Testing and Inspection
Quality control is an essential part of the manufacturing process. HDPE fittings undergo a variety of tests to ensure they meet the necessary standards for strength, leak resistance, and overall quality. Some of the tests performed include:
- Pressure Testing: To ensure the fittings can handle high-pressure conditions without failing.
- Dimensional Testing: To verify that the fittings meet precise size specifications.
- Visual Inspection: To check for defects, cracks, or inconsistencies in the fittings.
6. Marking and Branding
Once the fittings pass all necessary tests, they are marked with relevant information, including the manufacturer’s brand, the type of fitting, and the material grade. This marking helps with identification and ensures that the fittings are traceable throughout their lifecycle.
7. Packaging and Shipping
The final step in the manufacturing process is packaging and shipping. HDPE fittings are carefully packed to prevent any damage during transportation. They are then shipped to distributors, contractors, or directly to customers for use in various construction and plumbing projects.
Advantages of HDPE Fittings
HDPE fittings are widely preferred for their numerous advantages, which make them suitable for a range of applications.
- Durability: HDPE fittings are resistant to corrosion, abrasion, and impact. They can withstand harsh environmental conditions, including UV rays and extreme temperatures.
- Chemical Resistance: HDPE is highly resistant to chemicals, making it ideal for use in industries where pipes are exposed to corrosive substances, such as chemical processing and wastewater treatment.
- Flexibility: HDPE fittings can bend and conform to the required shapes without breaking, making them ideal for complex piping systems.
- Leak-Free Connections: HDPE fittings provide leak-free joints when properly installed, thanks to the heat fusion method used for joining the fittings to the pipes.
- Eco-Friendly: HDPE is a recyclable material, contributing to sustainable and environmentally-friendly plumbing systems.
Conclusion
The manufacturing process of HDPE fittings involves several key steps, including material selection, molding, testing, and packaging. These fittings are made to be durable, flexible, and resistant to corrosion, making them an excellent choice for a wide variety of industries. Whether you’re installing a new plumbing system or replacing outdated pipes, HDPE fittings provide long-lasting and reliable performance.
Frequently Asked Questions (FAQs)
- What is the primary material used for HDPE fittings?
HDPE fittings are made from High-Density Polyethylene (HDPE), a strong, flexible plastic known for its resistance to chemicals, corrosion, and extreme temperatures. - What is the difference between injection molding and extrusion in HDPE fitting production?
Injection molding is used to create smaller, more intricate fittings by injecting molten HDPE into molds. Extrusion is used to produce larger, continuous fittings by forcing molten HDPE through a die. - How do I ensure a leak-free connection with HDPE fittings?
To ensure a leak-free connection, use the proper heat fusion method to join HDPE pipes and fittings. Follow manufacturer guidelines for temperature and pressure during installation. - Are HDPE fittings recyclable?
Yes, HDPE fittings are recyclable and environmentally friendly. Recycled HDPE can be reused to create new products or fittings, contributing to sustainability. - What industries commonly use HDPE fittings?
HDPE fittings are used in various industries, including water and gas distribution, sewage and wastewater treatment, agriculture, and chemical processing, due to their durability and resistance to chemicals.