Introduction
Brass fittings are essential components used in various industries for their durability, corrosion resistance, and aesthetic appeal. A closer look at the manufacturing process of brass fittings reveals the intricate techniques involved in transforming raw materials into high-quality finished products.
Raw Materials
The manufacturing process begins with the selection of high-quality raw materials, primarily copper and zinc alloys. Copper provides the base metal, while zinc is added in varying proportions to achieve specific brass compositions. The quality of these raw materials greatly influences the final product’s strength and performance.
Casting
The first step in the manufacturing process is casting. The raw materials are melted in a furnace at high temperatures, forming a liquid brass alloy. This molten metal is then poured into molds, which are shaped according to the desired fitting design. The brass alloy solidifies within the mold, taking its specific shape.
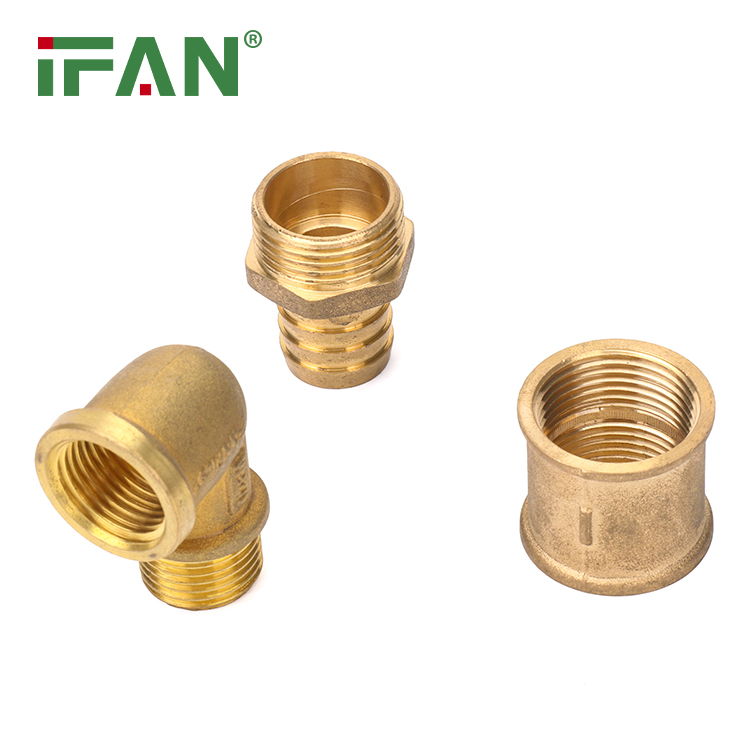
Machining
Once the casting process is complete, the brass fittings undergo machining operations to refine their shape and dimensions. This involves using precision tools, such as lathes, drills, and milling machines, to remove excess material and create intricate features. Machining ensures that the fittings meet precise specifications and tolerances.
Deburring and Cleaning
After machining, the fittings undergo deburring and cleaning processes. Deburring involves removing any rough edges or burrs that may be present on the surface of the fittings. This is achieved through various techniques, such as filing, grinding, or tumbling. The fittings are then thoroughly cleaned to remove any debris or contaminants that could affect their performance or appearance.
Surface Treatment
To enhance the aesthetics and longevity of brass fittings, various surface treatments are applied. Common surface treatments include polishing, plating, and coating. Polishing gives the fittings a smooth and shiny finish, while plating, such as nickel or chrome plating, provides enhanced corrosion resistance. Coatings, such as lacquer or epoxy, protect the fittings from tarnishing or discoloration.
Quality Control
Throughout the manufacturing process, rigorous quality control measures are implemented to ensure that the brass fittings meet industry standards and customer requirements. This includes conducting inspections, performing dimensional checks, and testing for strength, durability, and corrosion resistance. Any fittings that do not meet the required standards are rejected or reworked to maintain the highest quality.
Packaging and Distribution
Once the brass fittings have passed the quality control checks, they are carefully packaged to prevent damage during transportation. Proper packaging ensures that the fittings reach their destination in optimal condition. They are then distributed to wholesalers, retailers, or directly to end-users, ready for installation in various applications, such as plumbing, HVAC systems, or electrical connections.
Conclusion
The manufacturing process of brass fittings involves multiple steps, from the selection of high-quality raw materials to the final packaging and distribution. Each stage requires precision and expertise to ensure that the fittings meet the highest quality standards. Understanding this process provides a deeper appreciation for the craftsmanship and attention to detail involved in producing brass fittings that are reliable, functional, and visually appealing.
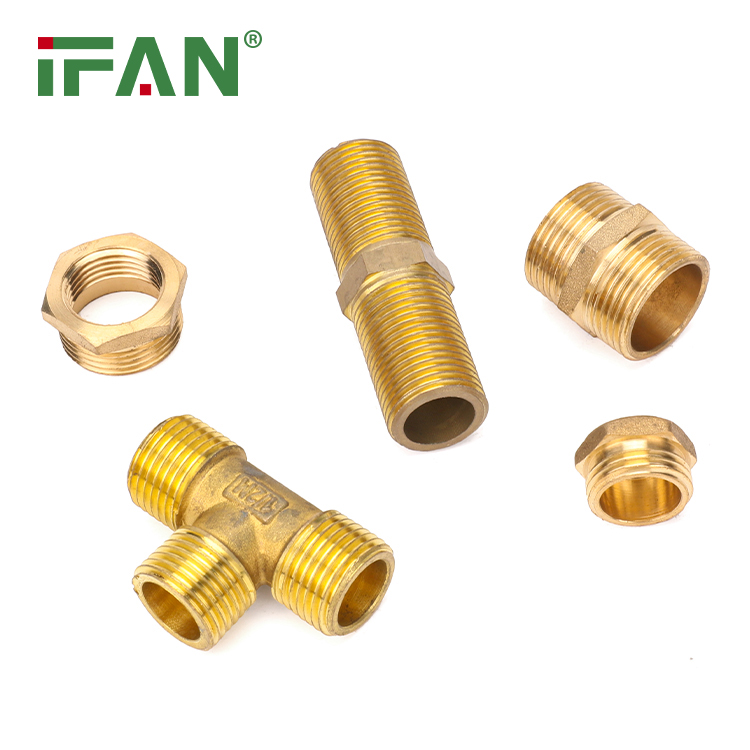