Description
The Importance of Properly Installing HDPE Fittings for Long-Lasting Performance
High-density polyethylene (HDPE) is widely used in a variety of piping applications due to its excellent physical properties, chemical resistance, and durability. It is highly adaptable to different installation methods, including butt fusion, electrofusion, and mechanical fittings. However, even if HDPE fittings are well-designed and manufactured to the highest standards, improper installation can lead to leaks, system failures, and costly repairs. That’s why engineers and installers need to follow best practices to ensure the proper installation of HDPE fittings for long-lasting performance.
HDPE fittings are designed to provide a secure and leak-free connection between pipes, valves, and other components in piping systems. They come in various shapes and sizes, including elbows, tees, reducers, couplings, and flanges, to accommodate different system configurations and pressures. HDPE fittings can be made from the same material as the pipe or from a compatible material, such as brass or stainless steel, for added strength and versatility.
One of the key advantages of HDPE fittings is their ability to withstand high temperatures and pressures without degradation or failure. HDPE fittings are resistant to corrosion, abrasion, and chemicals, making them ideal for use in harsh environments and demanding applications. Their smooth and non-porous surface prevents the buildup of scale, biofilm, or debris, which can reduce flow and cause blockages.
To achieve the full potential of HDPE fittings, proper installation is critical. This involves several key steps, such as preparing the pipe ends, selecting the correct fitting size and type, aligning the components, and applying the right amount of heat or pressure during fusion. For example, if the fusion temperature is too low, the fusion joint may be weak or incomplete, leading to leaks or failure. If the pressure is too high, the fitting may deform or crack, compromising its integrity.
By following industry standards and guidelines, installers can ensure the proper installation of HDPE fittings and avoid costly mistakes. They can also benefit from the long-lasting performance and reliability of HDPE fittings, which can reduce maintenance and replacement costs, increase system uptime, and improve productivity.
In conclusion, HDPE fittings offer many advantages over traditional piping materials, such as PVC, copper, or steel. They are lightweight, flexible, and easy to install, making them ideal for various industries, such as water, gas, mining, and agriculture. However, to reap the full benefits of HDPE fittings, proper installation is critical. This requires knowledge, skill, and attention to detail, as well as the use of quality tools and equipment. Therefore, it is important to work with experienced and qualified professionals who can ensure the proper installation of HDPE fittings and deliver long-lasting performance and value.
<a href=”https://www.ifanindus.com/contact-us/” rel=”noopener” target=”_blank”>Free Sample(Click Here to Get Free Sample)</a>
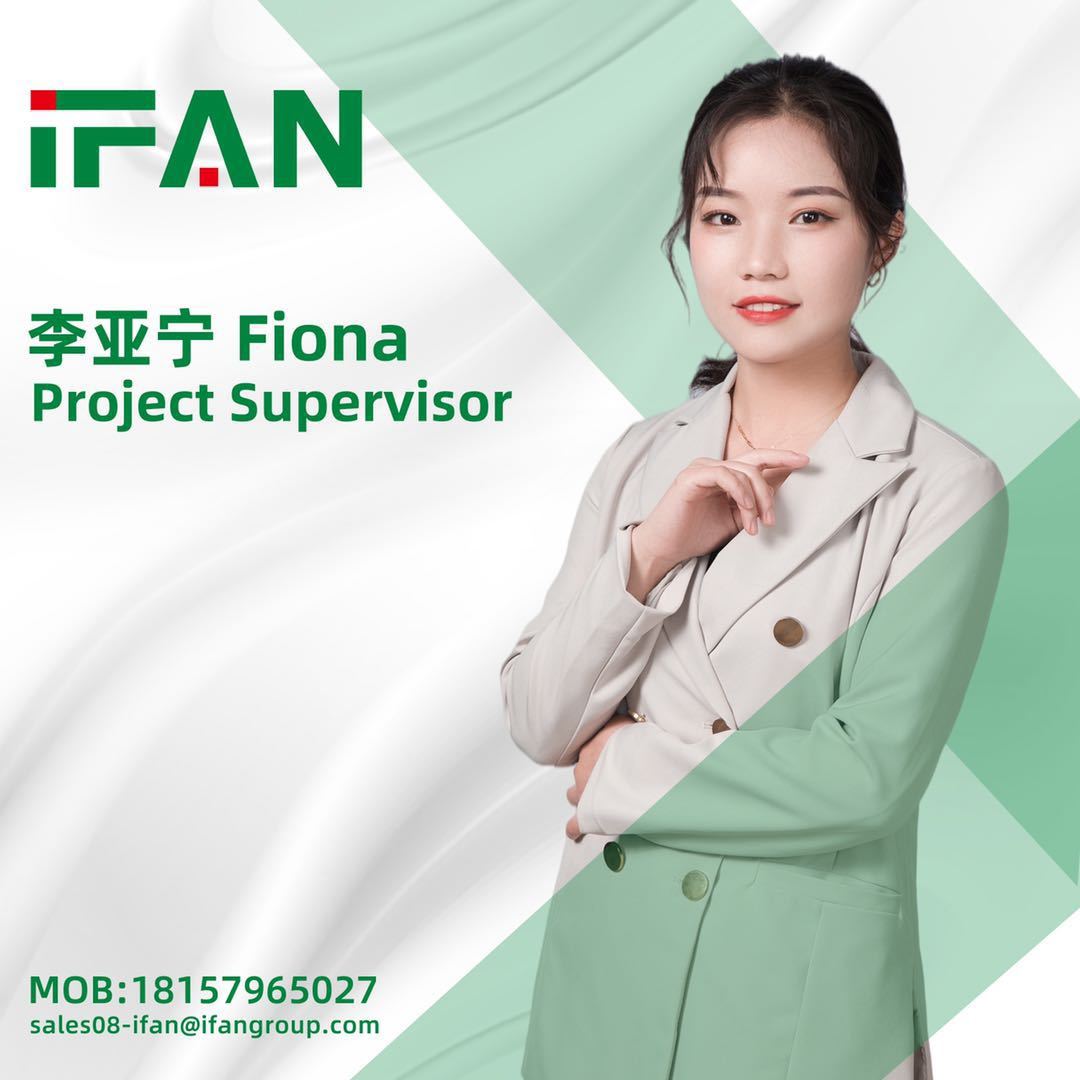