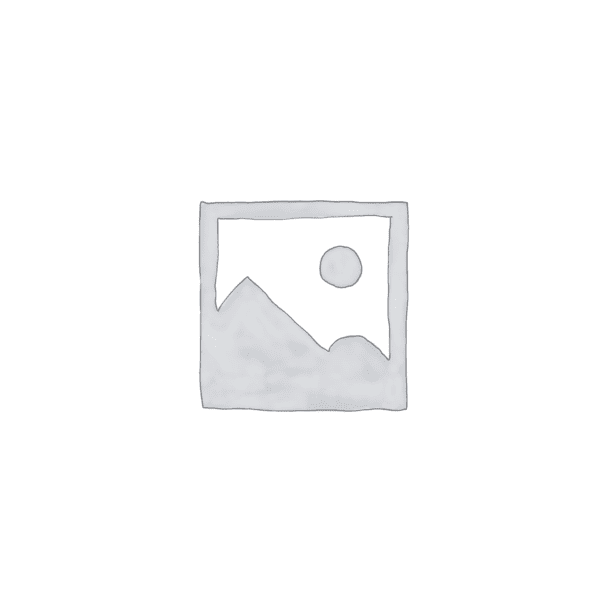
ASTM D3350 Common Problems and Solutions with HDPE Fittings
Whatsapp Us
Share
Description
IFAN factory 30+ years manufacture experience support color /size customization support free sample.Welcome to consult for catalog and free samples.This is our Facebook Website:www.facebook.com,Click to watch IFAN’s product video.Compared with Tomex products, our IFAN products from quality to price are your best choice, welcome to buy!
HDPE (High-Density Polyethylene) fittings are widely used in plumbing systems, industrial applications, water distribution, and other piping networks due to their durability, resistance to corrosion, and ease of installation. However, like any other product, HDPE fittings are not immune to problems. Understanding the common issues that can arise with HDPE fittings and knowing how to address them is crucial for maintaining the longevity and efficiency of the system. This article will explore the common problems associated with HDPE fittings and their solutions.
1. Improper Installation
Problem:
Improper installation is one of the most common problems when working with HDPE fittings. If the fitting is not installed correctly, it can lead to leaks, poor performance, or system failure. Common installation errors include incorrect fusion welding, improper alignment, and insufficient tightening of bolts.
Solution:
To avoid improper installation, it is essential to follow the manufacturer’s guidelines and industry standards during the installation process. HDPE fittings are often joined using fusion welding, which requires specialized equipment and trained personnel. Ensure that the fusion process is done correctly, with proper alignment and pressure. Additionally, using the right tools and ensuring all components are tightly sealed will prevent installation errors.
2. Leakage at Connections
Problem:
Leaks are a significant concern when it comes to HDPE fittings, especially at connection points. Leakage can occur if the pipes and fittings are not properly fused or if the seals are damaged. This is often seen when the HDPE fittings are subjected to excessive pressure or harsh environmental conditions.
Solution:
To solve leakage issues, check that the HDPE fittings are correctly installed and properly fused to the pipes. Use the recommended fusion equipment and techniques to ensure that the bond between the fitting and the pipe is solid. It is also essential to check that seals are in good condition and free from any damage or wear. If necessary, replace damaged seals and ensure the fitting is properly aligned and tightened.
3. Cracking or Fractures
Problem:
HDPE fittings, while durable, can crack or fracture over time due to factors such as exposure to extreme temperatures, UV radiation, or physical stress. Cracking may occur more frequently in outdoor installations exposed to harsh weather conditions or UV rays.
Solution:
To prevent cracking, consider using UV-resistant coatings or protective sleeves for outdoor applications. Additionally, avoid exposing HDPE fittings to extreme temperatures, both hot and cold. In industrial settings where the fittings may experience high pressure or thermal cycling, it’s crucial to select HDPE fittings with appropriate pressure ratings and to monitor the system regularly for signs of wear and tear. If cracking occurs, replace the damaged fitting promptly to avoid further damage.
4. Brittleness in Cold Weather
Problem:
In colder climates, HDPE fittings can become brittle and prone to breaking, especially if they are exposed to freezing temperatures. This issue is more prominent in regions with long winters or where water temperatures frequently dip below freezing.
Solution:
To mitigate brittleness in cold weather, ensure that the HDPE fittings are rated for low temperatures. Use fittings specifically designed for cold environments, which can withstand freezing conditions without compromising their structural integrity. Additionally, consider insulating the piping system or burying pipes deeper underground to protect them from freezing. Regularly inspect the system for signs of damage caused by freezing.
5. Chemical Resistance Issues
Problem
Although HDPE is highly resistant to many chemicals, it may still be vulnerable to certain aggressive substances. Chemical resistance issues may arise if the fittings come into contact with solvents, acids, or other materials that are not compatible with HDPE.
Solution:
To address chemical resistance issues, it’s essential to understand the chemicals the HDPE fittings will be exposed to and select the right type of HDPE material accordingly. HDPE fittings are available in various grades, each designed to handle specific chemicals. Always verify the chemical compatibility of the HDPE fittings with the substances in use. If necessary, use additional protective coatings or linings to prevent chemical damage.
6. Expansion and Contraction
Problem:
HDPE fittings and pipes are susceptible to expansion and contraction due to temperature changes. This can lead to stress at the connections, causing leaks or failure of the system.
Solution:
To avoid issues related to expansion and contraction, it is essential to include expansion loops or flexible joints in the piping system. These components allow the system to expand and contract without causing damage to the fittings or pipes. In addition, using HDPE fittings that are specifically designed to accommodate temperature fluctuations can reduce the risk of expansion-related problems.
7. Wear and Tear from Abrasive Materials
Problem:
In some industrial applications, HDPE fittings may experience wear and tear from abrasive materials flowing through the pipes. This can result in damage to the inner surface of the fittings, leading to leaks or reduced efficiency.Solution:
To prevent wear and tear from abrasives, ensure that the system is designed to handle the type of material being transported. For systems carrying abrasive substances, consider using HDPE fittings with thicker walls or protective linings. It may also be beneficial to regularly inspect the system for signs of wear and replace fittings that show significant damage.
8. UV Degradation
Problem:
Exposure to UV radiation can cause HDPE fittings to degrade over time, leading to brittleness and cracks. This is a common issue in outdoor installations or applications where the fittings are exposed to direct sunlight for extended periods.
Solution:
To prevent UV degradation, use UV-resistant HDPE fittings or apply UV-resistant coatings to protect the material. In some cases, installing the fittings underground or in shaded areas can minimize UV exposure and extend their lifespan. Regular inspections and maintenance are also necessary to detect signs of UV damage early and replace the fittings before further issues arise.
Conclusion
HDPE fittings offer excellent durability and versatility in a wide range of applications. However, like any material, they are susceptible to certain problems that can affect the performance and longevity of the system. By understanding the common issues and their solutions, you can ensure that your HDPE fittings perform optimally and continue to provide reliable service. Regular maintenance, correct installation techniques, and the use of suitable materials for specific conditions are key to preventing problems with HDPE fittings.
Frequently Asked Questions (FAQs)
1. What causes leaks in HDPE fittings?
Leaks in HDPE fittings are usually caused by improper installation, damaged seals, or faulty fusion welding. Ensure that fittings are installed according to manufacturer guidelines to prevent leaks.
2. Can HDPE fittings be used in cold weather?
HDPE fittings can become brittle in extremely cold temperatures. To prevent this, use fittings rated for low temperatures and consider insulating pipes to protect them from freezing.
3. How can I prevent cracking in HDPE fittings?
Cracking can be prevented by using UV-resistant coatings for outdoor applications and selecting fittings with the appropriate pressure and temperature ratings for the specific environment.
4. Are HDPE fittings resistant to chemicals?
HDPE is resistant to many chemicals, but some aggressive substances can cause damage. Always verify the chemical compatibility of HDPE fittings before use in chemical applications.
5. How do I install HDPE fittings correctly?
Correct installation involves following the manufacturer’s fusion welding guidelines and ensuring proper alignment, pressure, and tightening of fittings. It’s important to use the correct fusion equipment and tools during installation.
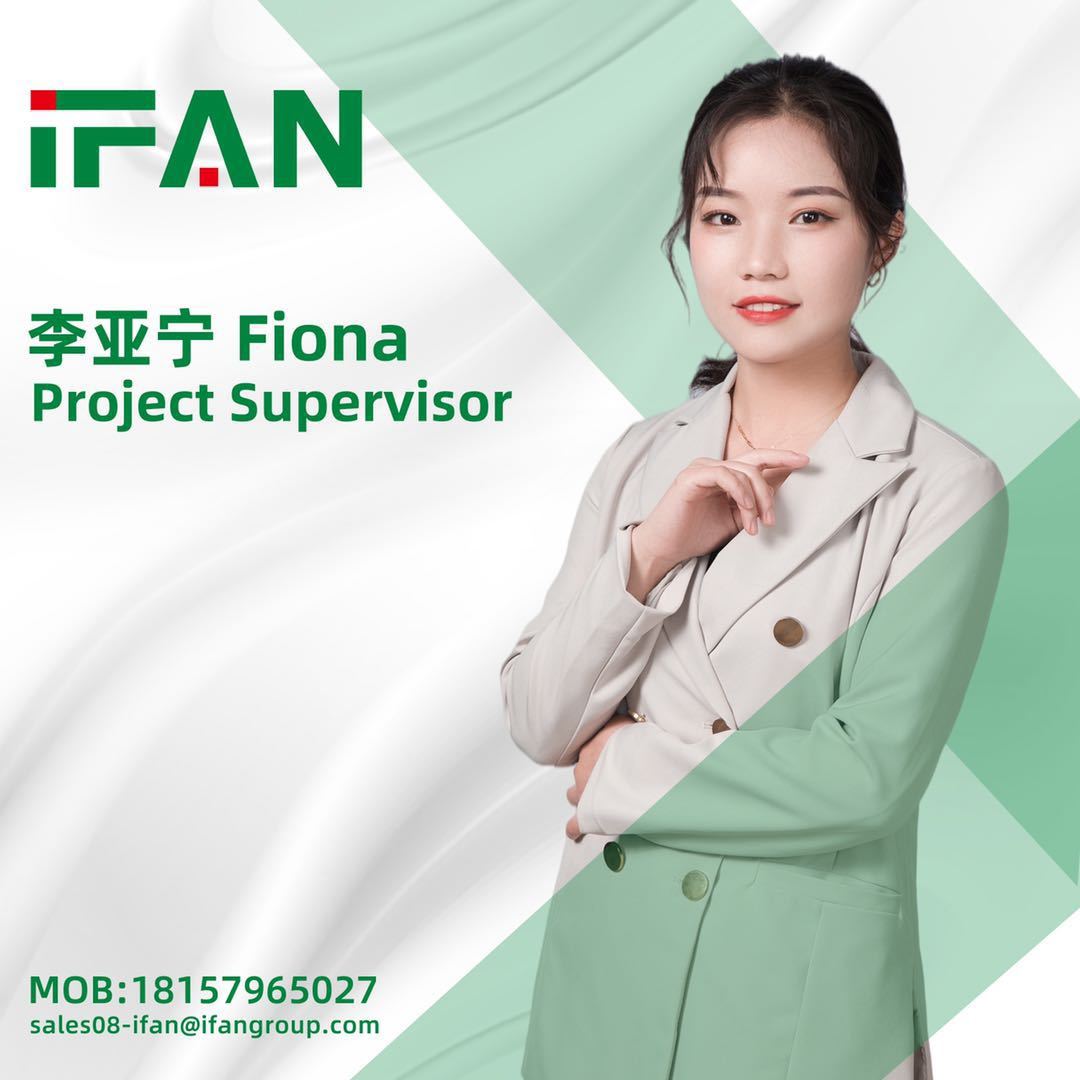