IFAN factory 30+ years manufacture experience support color /size customization support free sample.Welcome to consult for catalog and free samples.This is our Facebook Website:www.facebook.com,Click to watch IFAN’s product video.Compared with Tomex products, our IFAN products from quality to price are your best choice, welcome to buy!
High-Density Polyethylene (HDPE) fittings have become a key component in modern piping systems due to their exceptional durability, flexibility, and resistance to corrosion. Whether you’re building a residential, commercial, or industrial piping network, HDPE fittings offer a long-lasting and reliable solution. In this article, we will dive deep into what HDPE fittings are, why they are widely used, and how they compare to other options like PPR fittings, which are also popular in modern piping systems.
What Are HDPE Fittings?
HDPE fittings are components made from High-Density Polyethylene, a type of thermoplastic polymer known for its strength and resistance to environmental factors. These fittings are designed to connect HDPE pipes, which are commonly used in water supply, drainage systems, and gas pipelines. HDPE fittings come in various shapes such as elbows, tees, couplings, and reducers to suit different piping system configurations.
While HDPE fittings have become widely used in many industries, PPR fittings, made from Polypropylene Random Copolymer, have also gained popularity in plumbing systems. Both HDPE and PPR offer excellent advantages, but their application largely depends on the specific needs of the plumbing project.
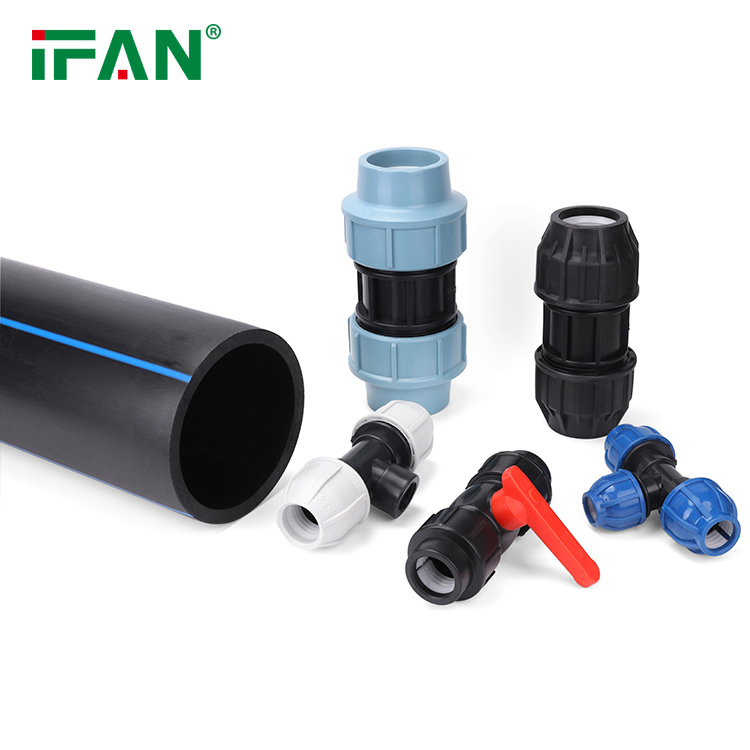
The Advantages of HDPE Fittings
- Long-Term Durability
HDPE fittings are known for their durability and can last for several decades with minimal maintenance. Unlike metal piping systems that can rust and deteriorate over time, HDPE fittings are resistant to corrosion, making them an ideal choice for plumbing systems exposed to harsh environments, moisture, or chemicals. This ensures that HDPE fittings provide a long-term, reliable solution for various applications.
- Corrosion Resistance
Corrosion is a common issue with traditional metal pipes, particularly when exposed to water or chemicals. HDPE fittings offer excellent resistance to corrosion, preventing common problems like leaks, blockages, and system failures. This characteristic makes them suitable for industries such as agriculture, water treatment, and gas distribution, where resistance to corrosion is vital.
- Flexibility and Ease of Installation
Another key advantage of HDPE fittings is their flexibility. HDPE pipes and fittings are highly flexible, allowing them to adapt to various installation configurations. This flexibility makes them easier to handle, even in challenging installations where pipes need to navigate around obstacles.
The installation process for HDPE fittings is also straightforward, with many systems relying on heat fusion to create leak-proof joints. The fusion process creates a seamless connection between the pipe and fitting, ensuring long-lasting performance and minimizing the chances of leaks.
- Chemical Resistance
HDPE fittings are known for their resistance to a wide range of chemicals. Whether the system needs to carry acidic, alkaline, or even saline water, HDPE fittings maintain their structural integrity and performance. This makes them an excellent choice for industrial applications where chemical exposure is common.
- Cost-Effectiveness
While HDPE fittings might have a higher upfront cost compared to other materials like PVC or PPR fittings, their long lifespan and resistance to wear make them more cost-effective in the long term. With fewer replacements and less maintenance, HDPE fittings help save on both installation and operational costs.
- Environmentally Friendly
HDPE is a recyclable material, making it an environmentally friendly option for piping systems. At the end of their life cycle, HDPE fittings can be repurposed into new products, helping reduce waste and conserve resources. The longevity of HDPE fittings also means fewer replacements, further minimizing the environmental impact.
HDPE vs. PPR Fittings
Both HDPE and PPR fittings are widely used in modern plumbing systems, but they serve different purposes and offer distinct advantages. While HDPE fittings are known for their exceptional resistance to corrosion, PPR fittings are known for their high resistance to pressure and temperature.
PPR fittings, made from Polypropylene Random Copolymer, are typically used in hot and cold water systems, as well as heating systems. They are ideal for domestic and commercial plumbing systems, particularly where hot water is involved. PPR fittings are often preferred for their smooth surface, which ensures that the flow of water remains uninterrupted.
On the other hand, HDPE fittings are better suited for larger-scale applications where resistance to environmental conditions like UV exposure, corrosion, and harsh chemicals is required. While both materials offer excellent benefits, the choice between HDPE and PPR often comes down to the specific needs of the plumbing system.
Applications of HDPE Fittings
HDPE fittings are used in a variety of applications, both residential and industrial. Some common uses include:
- Water Supply Systems: HDPE fittings are often used in municipal water supply networks due to their resistance to corrosion and durability.
- Irrigation Systems: Agriculture and irrigation systems benefit from HDPE’s flexibility and resistance to harsh chemicals in fertilizers and pesticides.
- Gas Distribution: HDPE fittings are widely used in natural gas pipelines because of their ability to withstand pressure and environmental wear.
- Sewerage and Drainage: HDPE’s resistance to corrosion makes it ideal for sewerage and drainage systems, even in areas with high moisture levels.
Maintenance of HDPE Fittings
One of the primary reasons for choosing HDPE fittings in plumbing systems is their low-maintenance nature. Unlike metal pipes, which require frequent inspections and maintenance due to rust or leaks, HDPE fittings are resistant to corrosion and wear.
The fusion joint process ensures that the system remains leak-free for years. In addition, since HDPE is resistant to freezing and thawing, the fittings are less likely to crack or break in cold weather, making them suitable for a wide range of climates.
Conclusion
HDPE fittings are a versatile, durable, and cost-effective solution for modern plumbing systems. Whether you’re installing a water supply system, irrigation system, or industrial gas pipeline, HDPE fittings offer long-term performance and reliability. Their ability to resist corrosion, chemicals, and environmental factors makes them an ideal choice for both residential and commercial applications. While PPR fittings are also a great option for hot and cold water systems, HDPE fittings stand out for their durability, flexibility, and environmental benefits.
Frequently Asked Questions (FAQs)
1. What are HDPE fittings made of?
HDPE fittings are made from High-Density Polyethylene, a thermoplastic polymer known for its strength, flexibility, and resistance to corrosion.
2. Can HDPE fittings be used for hot water systems?
Yes, HDPE fittings can be used in hot water systems, but they are better suited for applications where environmental resistance, flexibility, and durability are the primary concerns.
3. What is the difference between HDPE and PPR fittings?
HDPE fittings are better suited for applications exposed to harsh chemicals and environmental conditions, while PPR fittings are typically used in hot and cold water systems, offering high resistance to pressure and temperature.
4. How long do HDPE fittings last?
HDPE fittings can last for over 50 years with minimal maintenance, making them an excellent long-term investment for plumbing systems.
5. Are HDPE fittings environmentally friendly?
Yes, HDPE fittings are recyclable and have a long lifespan, which helps reduce material waste and environmental impact.