Introduction
As the demand for clean water continues to rise, deep wells have become a crucial source of water supply in many regions. To ensure the efficiency and longevity of deep well systems, the choice of piping materials is vital. Polypropylene Random Copolymer (PPR) pipes are increasingly being recommended for deep well applications due to their unique properties and advantages. This article delves into the benefits of using PPR pipes and fittings in deep well systems, their installation considerations, and best practices for maintenance.
Understanding PPR Pipes
What are PPR Pipes?
PPR pipes are manufactured from Polypropylene Random Copolymer, a thermoplastic material known for its strength, durability, and resistance to various environmental factors. These pipes are widely used in plumbing, heating, and industrial applications, making them a preferred choice for water transportation in deep well systems.
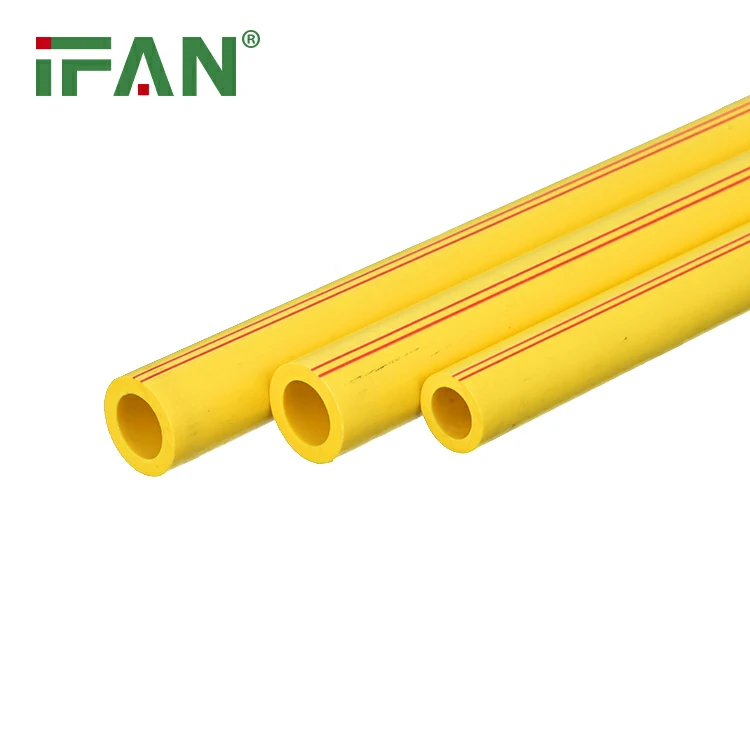
Key Features of PPR Pipes
- Durability: PPR pipes boast a lifespan of over 50 years, making them suitable for long-term applications. Their robust construction enables them to withstand high pressures and temperatures, essential for deep well systems.
- Corrosion Resistance: Unlike metal pipes, PPR pipes do not rust or corrode. This property ensures that the water remains uncontaminated, which is particularly important for drinking water applications.
- Leak-Free Joints: The jointing technology used in PPR pipes allows for seamless connections, significantly reducing the risk of leaks. This is crucial in deep well applications where water loss can lead to significant wastage and operational costs.
- Lightweight and Easy to Handle: PPR pipes are lightweight, making them easy to transport and install. This feature can lead to reduced labor costs and expedited installation times.
- Eco-Friendly: PPR pipes are fully recyclable and produced with minimal environmental impact. Their use contributes to sustainable water management practices.
Why Choose PPR Pipes for Deep Wells?
Enhanced Performance
PPR pipes are engineered to perform well under the demanding conditions often found in deep well applications. Their ability to withstand high pressure and temperature fluctuations makes them an ideal choice for transporting water from deep underground sources.
Improved Water Quality
The non-corrosive nature of PPR pipes ensures that the water remains clean and free from contaminants. This is especially important in deep well systems where water quality is paramount for public health. PPR pipes prevent the leaching of harmful substances, ensuring that the water supplied is safe for consumption.
Cost-Effectiveness
Although the initial investment in PPR pipes may be higher than traditional materials, the long-term savings associated with reduced maintenance and replacement costs make them a financially sound choice. Their durability means fewer repairs and replacements over time, leading to significant cost savings for deep well operators.
Recommended PPR Fittings for Deep Well Applications
Types of PPR Fittings
When installing PPR pipes in deep well systems, selecting the appropriate fittings is crucial for ensuring a reliable and efficient water transport system. Common types of PPR fittings include:
- Elbows: Used to change the direction of the piping, elbows are essential for navigating around obstacles in deep well installations.
- Tees: These fittings allow for branching off the main pipeline, enabling connections to additional water sources or distribution lines.
- Reducers: Used to connect pipes of different diameters, reducers are important for transitioning between various pipe sizes in deep well systems.
- Couplings: Couplings are used to connect two lengths of PPR pipe, providing a secure and leak-free joint.
- End Caps: End caps are used to seal the end of a PPR pipe, preventing any water loss and ensuring the integrity of the system.
Importance of Quality Fittings
Using high-quality PPR fittings is just as important as selecting the right pipes. Quality fittings ensure that the system operates efficiently and minimizes the risk of leaks. When choosing fittings, look for those that are specifically designed for PPR pipes and meet relevant industry standards.
Installation Considerations for PPR Pipes in Deep Wells
Planning the Installation
Proper planning is essential for the successful installation of PPR pipes in deep well systems. Consider the following factors:
- Depth of the Well: Assess the depth of the well and the pressure requirements for the water to be transported. This will help determine the appropriate pipe diameter and thickness.
- Water Quality: Test the water quality to ensure that PPR pipes are suitable for the specific conditions. This includes checking for any chemicals or contaminants that may affect the integrity of the pipes.
- Local Regulations: Familiarize yourself with local regulations and codes regarding deep well installations. Ensure that all materials used comply with these standards.
Installation Best Practices
- Use Proper Tools: Ensure that the right tools are used for cutting and joining PPR pipes. Specialized tools designed for PPR pipe installation will help achieve clean cuts and secure joints.
- Follow Manufacturer Guidelines: Always adhere to the manufacturer’s guidelines for installation and handling of PPR pipes and fittings. This will ensure optimal performance and longevity.
- Check for Leaks: After installation, conduct thorough testing for leaks. This step is crucial to ensure that the system is functioning correctly and to prevent water loss.
- Insulate Pipes: In areas with extreme temperatures, consider insulating PPR pipes to prevent damage from freezing or excessive heat.
Maintenance of PPR Pipes in Deep Well Systems
Regular Inspections
Conducting regular inspections of PPR pipes and fittings is essential for maintaining their performance in deep well applications. Look for signs of wear, damage, or leaks, and address any issues promptly to prevent further complications.
Cleaning and Flushing
Periodically cleaning and flushing the system can help remove any sediment or buildup that may affect water quality and flow rates. Ensure that the cleaning process is compatible with PPR pipes to avoid damage.
Monitor Water Quality
Regular testing of water quality is crucial for ensuring that the water supplied from deep wells remains safe for consumption. Monitor for any changes in taste, odor, or appearance, and investigate any concerns promptly.
Conclusion
The use of PPR pipes and fittings in deep well applications offers numerous advantages, including durability, corrosion resistance, and improved water quality. As the demand for clean water continues to grow, it is essential to adopt reliable and efficient materials for water transport systems. PPR pipes stand out as a cost-effective and sustainable solution for deep well installations. By following best practices for installation and maintenance, operators can ensure the longevity and performance of their deep well systems.
FAQs
- What are PPR pipes used for?
- PPR pipes are used for transporting hot and cold water in various applications, including plumbing, heating, and deep well systems.
- How long do PPR pipes last?
- PPR pipes can last over 50 years with proper installation and maintenance, making them a long-term solution for water transport.
- Are PPR pipes safe for drinking water?
- Yes, PPR pipes are designed to meet international standards for potable water systems, ensuring the safe transport of drinking water.
- What types of fittings are used with PPR pipes?
- Common fittings include elbows, tees, reducers, couplings, and end caps, all designed to create secure and leak-free connections.
- Can PPR pipes be used in extreme temperatures?
- PPR pipes are suitable for a wide range of temperatures, but it is advisable to insulate them in areas with extreme heat or cold to prevent damage.