Introduction
In the face of rapid urbanization, the demand for sustainable and efficient housing solutions has never been greater. Urban housing projects must address the needs of growing populations while ensuring that infrastructure is robust and reliable. One of the critical components of these projects is the plumbing system, where the choice of materials can significantly impact the overall quality and longevity of the housing development. Polypropylene Random Copolymer (PPR) pipes have emerged as a preferred solution in urban housing projects due to their numerous advantages. This report will explore the PPR pipe supply scheme for urban housing projects, detailing its benefits, implementation strategies, and long-term impact on the community.
Understanding PPR Pipes
What are PPR Pipes?
PPR pipes are made from polypropylene, a thermoplastic polymer known for its durability and resistance to various environmental factors. These pipes are primarily used in plumbing systems for both hot and cold water applications. Their lightweight nature, combined with excellent thermal insulation properties, makes them an ideal choice for urban housing projects.
Benefits of PPR Pipes
- Durability: PPR pipes can last over 50 years with proper installation and maintenance, significantly reducing the need for replacements.
- Corrosion Resistance: Unlike metal pipes, PPR pipes do not rust or corrode, ensuring a safe and clean water supply for residents.
- Ease of Installation: The lightweight nature of PPR pipes simplifies the installation process, reducing labor costs and time.
- Thermal Insulation: PPR pipes have excellent thermal insulation properties, minimizing heat loss in hot water systems and preventing condensation in cold water systems.
- Cost-Effectiveness: Although the initial investment may be higher than some alternatives, the long-term savings in maintenance and replacement costs make PPR pipes a wise choice for urban housing projects.
The Need for PPR Pipes in Urban Housing Projects
Urbanization Challenges
As cities expand, urban housing projects face several challenges, including:
- Increased Population Density: Rapid urbanization leads to overcrowding, necessitating the construction of more housing units.
- Aging Infrastructure: Many existing plumbing systems in urban areas are outdated and prone to leaks, affecting water quality and availability.
- Environmental Concerns: Urban housing projects must prioritize sustainable practices to minimize their ecological footprint.
The Role of PPR Pipes
PPR pipes address these challenges by providing a reliable and sustainable plumbing solution. Their durability and resistance to corrosion ensure that urban housing projects can deliver safe and clean water to residents, while their lightweight and easy installation features contribute to faster project completion times.
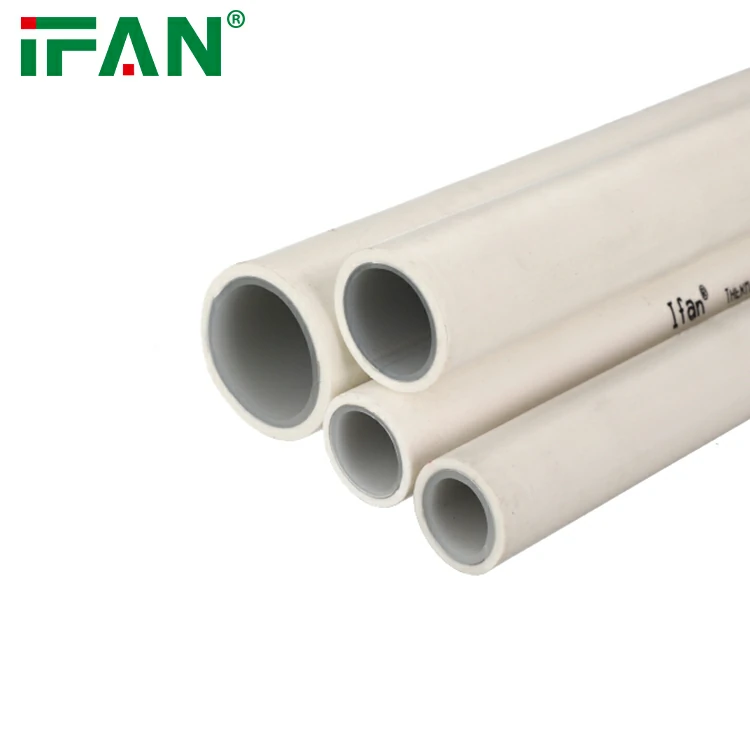
Implementation of the PPR Pipe Supply Scheme
Project Planning
The successful implementation of a PPR pipe supply scheme for urban housing projects begins with thorough project planning. Key steps include:
- Assessment of Needs: Conducting a comprehensive assessment of the plumbing requirements for the housing project, including water supply and drainage systems.
- Budget Allocation: Allocating a budget for the procurement of PPR pipes and related materials, considering both initial costs and long-term savings.
- Supplier Selection: Identifying reputable suppliers of PPR pipes, such as Lina Gabion and PPR Pipe Plastic Factory PLC, that offer high-quality products and reliable delivery.
Procurement Process
Once the project planning phase is complete, the procurement process can begin. This involves:
- Request for Proposals (RFPs): Issuing RFPs to potential suppliers to obtain competitive pricing and delivery timelines for PPR pipes.
- Supplier Evaluation: Evaluating suppliers based on quality, cost, delivery capabilities, and past performance in similar projects.
- Contract Negotiation: Negotiating contracts with selected suppliers to ensure favorable terms and conditions for the supply of PPR pipes.
Installation and Quality Assurance
After procurement, the next phase involves the installation of PPR pipes in the urban housing project. This includes:
- Training and Certification: Providing training for installation teams to ensure proper handling and installation of PPR pipes, adhering to industry standards.
- Quality Control Measures: Implementing quality control measures throughout the installation process to ensure the integrity and reliability of the plumbing system.
- Final Inspection: Conducting a final inspection of the installed PPR pipes to ensure compliance with project specifications and standards.
Long-Term Impact of PPR Pipes in Urban Housing Projects
Improved Living Conditions
The use of PPR pipes in urban housing projects significantly enhances the living conditions for residents. Benefits include:
- Reliable Water Supply: PPR pipes ensure a consistent and reliable water supply, reducing instances of leaks and water shortages.
- Enhanced Water Quality: The corrosion resistance of PPR pipes prevents contamination, ensuring that residents have access to clean and safe drinking water.
- Lower Maintenance Costs: The durability of PPR pipes translates to lower maintenance costs for housing authorities and residents, allowing for better allocation of resources.
Environmental Sustainability
PPR pipes contribute to the sustainability of urban housing projects in several ways:
- Reduced Waste: The longevity of PPR pipes minimizes the need for frequent replacements, reducing waste generated by discarded plumbing materials.
- Energy Efficiency: The thermal insulation properties of PPR pipes help maintain water temperatures, reducing energy consumption in heating systems.
- Recyclability: PPR pipes are recyclable, further minimizing their environmental impact at the end of their life cycle.
Case Studies: Successful Implementation of PPR Pipe Supply Schemes
Example 1: Urban Renewal Project in [City Name]
In [City Name], an urban renewal project successfully integrated PPR pipes into its plumbing systems. The project involved the installation of PPR pipes in over 500 housing units, resulting in improved water supply reliability and significant cost savings for the housing authority.
Example 2: Affordable Housing Initiative in [City Name]
An affordable housing initiative in [City Name] utilized PPR pipes to enhance the plumbing infrastructure of new housing developments. The project demonstrated how PPR pipes could improve living conditions for low-income families while promoting sustainable construction practices.
Conclusion
The PPR pipe supply scheme for urban housing projects represents a significant advancement in the pursuit of sustainable and efficient plumbing solutions. By addressing the challenges posed by urbanization, PPR pipes enhance the quality of life for residents while promoting environmental sustainability. The successful implementation of this supply scheme requires thorough planning, effective procurement, and quality assurance measures. As urban housing projects continue to evolve, the adoption of PPR pipes will play a crucial role in shaping the future of sustainable urban living.
FAQs
1. What are the advantages of using PPR pipes in urban housing projects?
PPR pipes offer several advantages, including durability, corrosion resistance, lightweight construction, thermal insulation properties, and cost-effectiveness.
2. How long do PPR pipes typically last?
PPR pipes can last over 50 years when installed and maintained properly, making them a long-term solution for plumbing needs.
3. Are PPR pipes safe for drinking water?
Yes, PPR pipes are safe for drinking water as they do not leach harmful substances and are resistant to corrosion.
4. Can PPR pipes be used for both hot and cold water applications?
Yes, PPR pipes are suitable for both hot and cold water applications, making them versatile for various plumbing needs.
5. How can I ensure the quality of PPR pipes I purchase for my project?
To ensure quality, purchase PPR pipes from reputable manufacturers, check for industry certifications, and consult with professionals regarding installation standards.