IFAN factory 30+ years manufacture experience support color /size customization support free sample.Welcome to consult for catalog and free samples.This is our Facebook Website:www.facebook.com,Click to watch IFAN’s product video.Compared with Tomex products, our IFAN products from quality to price are your best choice, welcome to buy!
When it comes to designing and installing high-pressure water systems, the choice of materials is crucial for ensuring durability, safety, and long-term performance. Among the many options available, HDPE fittings (High-Density Polyethylene fittings) have become a popular choice in high-pressure water systems due to their impressive strength, resistance to corrosion, flexibility, and cost-effectiveness. In this article, we will explore why HDPE fittings are perfect for high-pressure water systems and how they outperform other materials in various applications.
What Are HDPE Fittings?
HDPE fittings are components made from High-Density Polyethylene, a thermoplastic polymer known for its strength and durability. These fittings are commonly used in water distribution, sewage, industrial piping, and other high-pressure applications. The material itself is highly resistant to environmental stress, chemical corrosion, and abrasion, making it an ideal choice for challenging environments.
Why HDPE Fittings Are Ideal for High-Pressure Water Systems
- Exceptional Strength-to-Weight Ratio
One of the key reasons why HDPE fittings are perfect for high-pressure water systems is their exceptional strength-to-weight ratio. Despite being lighter than metal fittings like steel or brass, HDPE fittings can withstand considerable pressure without compromising their structural integrity. The material’s molecular structure gives it the strength needed to handle high-pressure applications, all while remaining lightweight and easy to install.
This characteristic makes HDPE fittings particularly attractive in water distribution systems, where both the material’s ability to endure high pressure and the ease of handling are crucial. In many installations, HDPE fittings are able to handle pressures of up to 200 PSI (pounds per square inch) or more, making them suitable for a wide range of high-pressure systems.
- Corrosion Resistance
Unlike traditional metal fittings, HDPE fittings are highly resistant to corrosion. In high-pressure water systems, water is often exposed to various chemicals, minerals, and environmental factors that can cause metals to rust or degrade over time. HDPE fittings, on the other hand, are completely impervious to corrosion, ensuring long-term reliability and reduced maintenance costs.
In high-pressure systems, even small leaks or weaknesses in the piping can lead to significant damage. The corrosion-resistant nature of HDPE fittings ensures that the system will remain intact and efficient over time, even in harsh environments such as coastal areas with saltwater exposure or regions with highly acidic water.
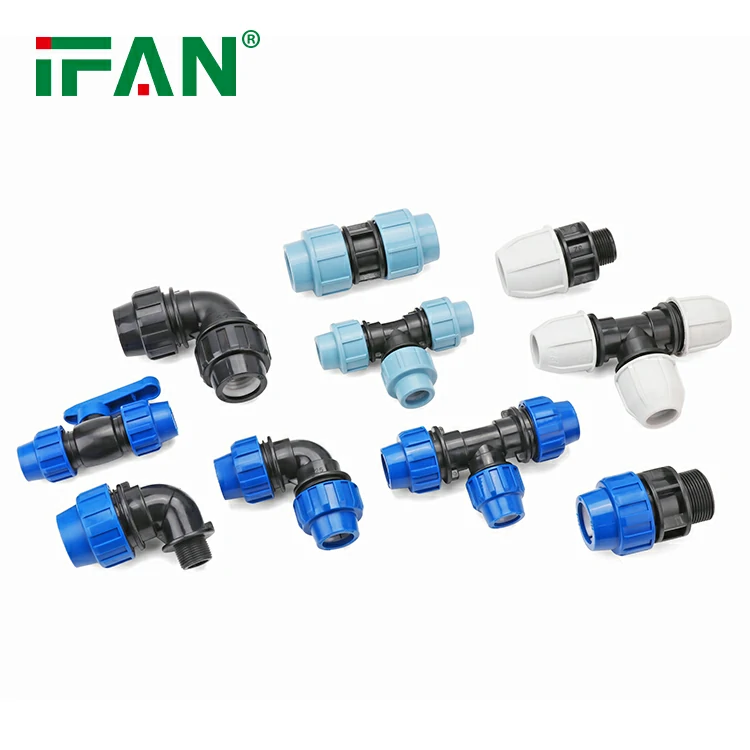
- Resistance to Abrasion
In high-pressure systems, water flow can sometimes carry sand, gravel, or other abrasive materials. HDPE fittings are incredibly resistant to abrasion, meaning they will not degrade or wear down when exposed to these abrasive elements. This resistance to abrasion is particularly beneficial for systems that involve the movement of water mixed with particulate matter, such as mining or wastewater treatment facilities.
Traditional metal fittings are more susceptible to wear and tear under abrasive conditions, which can result in leaks and the need for frequent replacements. HDPE fittings, with their abrasion-resistant properties, provide a more durable solution for high-pressure water systems.
- Flexibility and Impact Resistance
Another advantage of HDPE fittings in high-pressure water systems is their flexibility. Unlike metal fittings, which can become brittle and crack under stress or impact, HDPE fittings are flexible and able to absorb shocks without breaking. This flexibility is essential in systems that experience fluctuations in pressure, temperature changes, or even ground movement.
For example, in areas prone to earthquakes or ground shifts, HDPE fittings are less likely to crack or fail, ensuring that the piping system remains intact even under challenging conditions. This flexibility also helps HDPE fittings resist pressure surges that might otherwise cause metal fittings to rupture or fail.
- Cost-Effectiveness
In terms of both material and installation costs, HDPE fittings offer a significant cost advantage over traditional metal fittings. HDPE fittings are generally more affordable than their metal counterparts, such as copper, brass, or stainless steel. Moreover, their lightweight nature reduces transportation and handling costs.
The installation process for HDPE fittings is also simpler and faster than for metal fittings. HDPE fittings are typically joined using heat fusion, a process that creates a seamless, leak-proof connection without the need for welding, soldering, or threading. This reduces labor costs and installation time, making HDPE fittings a cost-effective solution for high-pressure water systems.
- Low Maintenance Requirements
One of the most attractive features of HDPE fittings is their low maintenance requirements. Due to their resistance to corrosion, abrasion, and environmental stress, HDPE fittings require minimal upkeep over their lifespan. This reduces the overall operational costs of a high-pressure water system, as the need for repairs, replacements, and frequent inspections is greatly diminished.
In comparison, metal fittings often require ongoing maintenance to prevent corrosion and ensure the integrity of the system. Over time, the cost of maintaining a metal-based high-pressure water system can add up, making HDPE fittings a more economical long-term choice.
- Environmental Impact
HDPE fittings are also a more environmentally friendly option for high-pressure water systems. HDPE is a recyclable material, which means that at the end of its lifespan, HDPE fittings can be repurposed rather than sent to a landfill. Additionally, HDPE fittings require less energy to produce compared to metal fittings, making them a more sustainable option for water infrastructure projects.
Many municipalities and companies today are prioritizing environmentally responsible materials in their infrastructure projects, and HDPE fittings align well with these sustainability goals.
Key Applications of HDPE Fittings in High-Pressure Water Systems
- Municipal Water Distribution
HDPE fittings are commonly used in municipal water distribution systems where high pressures are needed to ensure that water can reach homes and businesses efficiently. The material’s strength and resistance to corrosion make it an ideal choice for large-scale water infrastructure projects. - Industrial Applications
In industries such as mining, oil and gas, and agriculture, high-pressure water systems are essential for operations such as pumping, irrigation, and cooling. HDPE fittings are often used in these environments due to their ability to handle high pressures and resist chemical degradation. - Fire Suppression Systems
Fire suppression systems require high-pressure water to be delivered rapidly to extinguish fires. HDPE fittings are used in these systems because they can handle the pressure while offering reliable and long-lasting performance. - Wastewater Treatment Plants
In wastewater treatment plants, high-pressure systems are needed to move water through various stages of filtration and treatment. HDPE fittings are perfect for these applications due to their corrosion resistance and ability to handle both high pressure and abrasive materials.
Conclusion
HDPE fittings are an excellent choice for high-pressure water systems due to their exceptional strength, corrosion resistance, flexibility, and cost-effectiveness. Whether you’re working on a municipal water distribution project, an industrial application, or a fire suppression system, HDPE fittings offer numerous advantages over traditional metal fittings. With lower installation and maintenance costs, as well as a longer lifespan, HDPE fittings prove to be the ideal solution for modern, high-pressure water systems.
Frequently Asked Questions (FAQs)
1. What is the maximum pressure that HDPE fittings can withstand?
HDPE fittings can typically withstand pressures of up to 200 PSI or more, depending on the specific grade and design of the fitting. They are suitable for most high-pressure water applications.
2. Are HDPE fittings resistant to chemicals?
Yes, HDPE fittings are highly resistant to a wide range of chemicals, including acids, alkalis, and solvents, making them ideal for industrial applications where chemicals are present in the water.
3. Can HDPE fittings be used for hot water systems?
Yes, HDPE fittings can be used for hot water systems, but it’s important to ensure that the temperature of the water does not exceed the material’s maximum temperature tolerance, which is typically around 140°F (60°C) for most HDPE materials.
4. How long do HDPE fittings last?
HDPE fittings can last for decades, with some systems lasting 50 years or more without significant degradation, provided they are installed and maintained properly.
5. Are HDPE fittings difficult to install?
No, HDPE fittings are relatively easy to install compared to metal fittings. They are typically joined using heat fusion, which creates a strong, leak-proof bond without the need for welding or threading.